28.12.2019
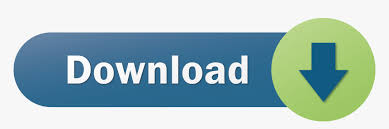
Clean Slate 2.0.367 serial key or number

Clean Slate 2.0.367 serial key or number
Hilti 2008 Product Technical Guide R021 1
This document was uploaded by user and they confirmed that they have the permission to share it. If you are author or own the copyright of this book, please report to us by using this DMCA report form. Report DMCA
Overview
Download & View Hilti 2008 Product Technical Guide R021 1 as PDF for free.
More details
- Words: 205,434
- Pages: 452
North American Product Technical Guide
A guide to specification and installation
Hilti. Outperform. Outlast. P.O. Box 21148, Tulsa, OK 74121 • Hilti, Inc. (US) 1-800-879-8000 www.us.hilti.com • Servicio al Cliente en español 1-800-879-5000 • Hilti (Canada) Corporation 1-800-363-4458 www.ca.hilti.com • Hilti is an equal opportunity employer Hilti is a registered trademark of Hilti, Corp. ©Copyright 2006 by Hilti, Inc. • H440 • 3004711 • 1/08 HA The data contained in this literature was current as of the date of publication. Updates and changes may be made based on later testing. If verification is needed that the data is still current, please contact the Hilti Technical Support Specialists at 1-800-879-8000. All published load values contained in this literature represent the results of testing by Hilti or test organizations. Local base materials were used. Because of variations in materials, on-site testing is necessary to determine performance at any specific site. Laser beams represented by red lines in this publication. Printed in the United States
*ISO 14001 US Only
2008 Edition
Prod_Tech_Guide_Cover_2008.qxd:MI_Kapitel_5_en.qxd
12/29/07
2:16 PM
Page 4
Hilti Product Technical Guide
P R O F I S
PROFIS: The World’s Most Powerful Anchor Design Software • Easy to Learn – Start working in just minutes • Fast and Powerful – Produce detailed designs quickly • Specify with Confidence – The largest number of approvals and latest design codes No charge. Download now at www.us.hilti.com or www.hilti.ca
Hilti Online • • • • • • •
Technical Library Design Centers Interactive Product Advisors Full-line Product Catalog Online Ordering Maps to Hilti locations “Contact Us” program to answer your questions
Firestop Systems When it comes to Life Safety and building code compliance, Hilti provides complete solutions with a wide range of products and unmatched technical support. • Firestop Systems Guides - Through Penetrations - Joint Penetrations • FACT Program • FS 411 • BASIC Training • Engineering Judgements • Firestop Design Center online at www.us.hilti.com or www.hilti.ca
Hilti Diaphragm Deck Design The Hilti Diaphragm Deck Design Program allows designers to quickly and accurately design roof deck and composite floor deck diaphragms. • Ability to design with innovative Hilti fasteners for frame and sidelap connection • Creates easy to use load tables with span ranges based on user input • Allows for different safety factors depending on load type, building code and field quality control • Direct link to Hilti website
MI – Industrial Pipe Support Technical Guide A guide to specifying the Hilti modular pipe support system for medium to heavy loads without welding. • MI System is the ideal solution for pipes up to 24 in. diameter • Reliable fastenings without welds • Easily installed
Hilti, Inc. (US) 1-800-879-8000 | www.us.hilti.com I en español 1-800-879-5000 I Hilti (Canada) Corp. 1-800-363-4458 I www.ca.hilti.com I Product Technical Guide 2008
01_Intro_.QXD:H440.06_0102 IntroGenInf.QXD
12/30/07
12:45 AM
Page 1
Hilti Product Technical Guide
Table of Contents Table of Contents
Introduction
1.0
2
Fastening Technology
2.0
3
Direct Fastening Systems
3.0
16
Anchoring Systems
4.0
128
Construction Chemicals
5.0
390
Installation Systems
6.0
404
Reference
7.0
438
Hilti, Inc. (US) 1-800-879-8000 | www.us.hilti.com I en español 1-800-879-5000 I Hilti (Canada) Corp. 1-800-363-4458 I www.hilti.ca I Product Technical Guide 2008 1
01_Intro_.QXD:H440.06_0102 IntroGenInf.QXD
12/30/07
12:45 AM
Page 2
Hilti Product Technical Guide
1.0 Introduction 1.1 About Published Load Values
1.3 Our Purpose
The Product Technical Guide is intended to supplement the
We passionately create enthusiastic customers and build a better future!
Hilti Product Catalog with technical information for the designer or specifier. Technical data presented herein was current as of the date of publication (see back cover). Load values are based on testing and analytical calculations by Hilti or by contracted testing laboratories using testing procedures and construction materials representative of current practice in North America. Load values obtained from testing represent the average results of multiple identical samples. Variations in base materials such as concrete and local site conditions require on-site testing to determine actual performance at any specific site. Data may also be based on national standards or professional research and analysis. Note that design values published in reports issued by approval agencies (e.g., ICC-ES, COLA, etc.) may differ from those contained in this Product Technical Guide. For information regarding updates and changes, please contact Hilti,Inc. (US) Technical Support at 1-800-879-8000 or Hilti (Canada) Corporation at 1-800-363-4458.
1.2 Units Technical data is provided in both fractional (Imperial) and metric units. Metric values are provided using the International System of units (SI) in observance the Metric Conversion Act of 1975 as amended by the Omnibus Trade and Competitiveness Act of 1988. Data for metric products, such as the HSL and HDA anchors, is provided in SI units with conversions to Imperial engineering units (inches, pounds, and so forth) given in parentheses. Data for fractional products (e.g. the Kwik Bolt 3) is provided in Imperial engineering units with the SI metric conversions shown in parentheses. Additional information may be found in Section 8.3.1 Metric Conversions and Equivalents, provided in this Product Technical Guide.
Enthusiastic Customers We create success for our customers by identifying their needs and providing innovative and value-adding solutions. Build a better future We embrace our responsibility towards society and environment.
1.4 Our Quality System Hilti is one of a select group of North American companies to receive the ISO 9001 and ISO 14001 Certifications. This recognition of our commitment to quality ensures our customers that Hilti has the systems and procedures in place to maintain our position as the world market leader, and to continually evaluate and improve our performance. That’s Total Customer Satisfaction! For Technical Support, contact Hilti,Inc. (US) at 1-800-8798000 or Hilti (Canada) Corporation at 1-800-363-4458.
2 Hilti, Inc. (US) 1-800-879-8000 | www.us.hilti.com I en español 1-800-879-5000 I Hilti (Canada) Corp. 1-800-363-4458 I www.hilti.ca I Product Technical Guide 2008
01_Intro_.QXD:H440.06_0102 IntroGenInf.QXD
12/30/07
12:45 AM
Page 3
Fastening Technology
Base Materials 2.1 2.1.1 Base Materials for Fastening The design of modern buildings requires fastenings to be made in a variety of base materials. To meet this challenge, fastener manufacturers have developed many products specifically targeting certain types of base materials. The properties of the base material play a decisive role in the suitability and performance of a fastener. The designer must carefully match the type of fastener with the base material to obtain the desired results. There is hardly a base material in which a fastening cannot be made with a Hilti product.
2.1.2 Concrete Concrete is a mineral building material which is made from three basic ingredients; cement, aggregate and water. Special additives are also used to influence or change certain properties. Concrete has a relatively high compressive strength compared to its tensile strength. Thus, steel reinforcing bars are cast in concrete to carry the tensile forces, and this combination is referred to as reinforced concrete. Cement is the binding agent which combines with water and aggregate and hardens through the process of hydration to form concrete. Portland cement is the most common cement and is available in several different types, as outlined in ASTM C 150, to meet specific design requirements. The aggregates used in concrete consist of both fine aggregate (usually sand) and coarse aggregate graded by particle size. Different types of aggregates can be used to create concrete with specific characteristics. Normal weight concrete is generally made from crushed stone or gravel. Lightweight concrete is used when it is desirable to reduce the dead load on a structure or to achieve a superior fire rating for a floor structure. Lightweight aggregates are made from expanded clay, shale, slate or blast-furnace slag. Lightweight insulating concrete is used when thermal insulating properties are a prime consideration. Lightweight insulating aggregates are manufactured from perlite, vermiculite, blast-furnace slag, clay or shale. Sand lightweight concrete is made from lightweight aggregate and natural sand. All concrete with a unit weight between 85 and 115 pcf is considered to be structural lightweight concrete. The ASTM specification and unit weight for each of these concretes is summarized as follows:
ASTM Concrete Type Normal Weight Sand Lightweight All Lightweight Lightweight Insulating Concrete
Aggregate Grading Specification
Concrete Unit Weight pcf
ASTM C 33 ASTM C 330 ASTM C 330 ASTM C 332
145-155 105-115 85-110 15-90
The type and mechanical properties of concrete aggregate have a major influence on the behavior of drill bits used to drill anchor holes. The harder the aggregates cause higher bit wear and reduced drilling performance. The hardness of concrete aggregate can also affect the load capacity of power-actuated fasteners and anchors. Driven fasteners or studs can generally penetrate “soft” aggregates (shale or limestone), but hard aggregates (like granite) near the surface of the concrete can adversely affect the penetration of a fastener or stud and reduce its load capacity. The effect of aggregate mechanical properties on anchor performance is less well understood, although in general harder/denser aggregates such as granite tend to result in higher concrete cone breakout loads, whereas lightweight aggregates produce lower tension and shear capacities. Values for the ultimate strength of fasteners in concrete are traditionally given in relation to the 28-day uniaxial compressive strength of the concrete (actual, not specified). Concrete which has cured for less than 28 days is referred to as green concrete. Aggregate type, cement replacements such as fly ash, and admixtures could have an effect on the capacity of some fasteners, and this may not be reflected in the concrete strength as measured in a uniaxial compression test. Generally, Hilti data reflects testing with common aggregates and cement types in plain, unreinforced concrete. In questionable cases, consult with Hilti Technical Support. In view of the significantly lower strength of green concrete (less than 28-day cure), it is recommended that anchors and power-actuated fastenings not be made in cast-in-place concrete which has cured for less than 7 days, unless site testing is performed to verify the fastening capacity. If an anchor is installed in green concrete, but not loaded until the concrete has achieved full cure, the capacity of the anchor can be based on the strength of the concrete at the time of loading. Power-actuated fastening capacity should be based on the concrete strength at the time of installation. Cutting through concrete reinforcement when drilling holes for anchors should be avoided. If this is not possible, the responsible design engineer should be consulted first.
Hilti, Inc. (US) 1-800-879-8000 | www.us.hilti.com I en español 1-800-879-5000 I Hilti (Canada) Corp. 1-800-363-4458 I www.hilti.ca I Product Technical Guide 2008 3
01_Intro_.QXD:H440.06_0102 IntroGenInf.QXD
12/30/07
12:45 AM
Page 4
Fastening Technology
2.1 Base Materials 2.1.3 Masonry Materials
8"
Masonry is a heterogeneous building material consisting of brick, block or clay tile bonded together using joint mortar. The primary application for masonry is the construction of walls which are made by placing masonry components in horizontal rows (course) and vertical rows (wythe). Masonry components are manufactured in a wide variety of shapes, sizes, materials and both hollow and solid configurations. These variations require that the selection of an anchoring or fastening system be carefully matched to the application and type of masonry material being used. As a base material, masonry generally has a much lower strength than concrete. The behavior of the masonry components, as well as the geometry of their cavities and webs, has a considerable influence on the ultimate load capacity of the fastening. When drilling holes for anchors in masonry with hollow cavities, care must be taken to avoid spalling on the inside of the face shell. This could greatly affect the performance of “toggle” type mechanical anchors whose length must be matched to the face shell thickness. To reduce the potential for spalling, holes should be drilled using rotation only (i.e. hammering action of the drill turned off).
2.1.3.1 Concrete Block Concrete block is the term which is commonly used to refer to concrete masonry units (CMU) made from Portland cement, water and mineral aggregates. CMUs are manufactured in a variety of shapes and sizes using normal weight and lightweight aggregates. Both hollow and solid load bearing CMUs are produced in accordance with ASTM C90. Nominal Width of Unit in. (mm)
Minimum face-shell ThicknessA in. (mm)
3 (76) and 4 (102) 6 (152)
Minimum web ThicknessA in. (mm)
3/4 (19)
3/4 (19)
1 (25)
1 (25)
8 (203)
1-1/4 (32)
1 (25)
10 (254)
1-3/8 (35) 1-1/4 (32)B
1-1/8 (29)
1-1/2 (38) 1-1/4 (32)B
1-1/8 (29)
≥12 (305)
7 5\8"
7 5\8"
8"
16"
Nominal Size (usually fictitious)
15 5\8"
Modular Size (actual)
CMU sizes generally refer to the nominal width of the unit (6”, 8”, 10” etc.). Actual dimensions are nominal dimensions reduced by the thickness of the mortar joint. Concrete block construction can be reinforced, whereby reinforcing bars are placed vertically in the cells and those cells are filled with grout to create a composite section analogous to reinforced concrete. If all cells, both unreinforced and reinforced, are filled with grout, the construction is referred to as fully grouted. If only the reinforced cells are grouted, the construction is referred to as partially grouted. Horizontal reinforcing may be placed in the wall via a bond beam, which is always grouted. Ladder reinforcement may also be placed in the mortar bed between courses. Grout typically conforms to ASTM C476 and has a compressive strength of at least 2,000 psi. Concrete masonry units have a compressive strength which may range from 1,250 to over 4,800 psi, although the maximum specified compressive strength of the assembled masonry will generally not exceed 3,000 psi. In general, both chemical and mechanical anchors may be used in grouted CMU. If voids are present or suspected, mechanical anchors should not be used, and chemical anchors should only be installed in conjunction with a screen tube to prevent uncontrolled flow of the bonding material. In ungrouted CMU, anchor strength is generally assumed to be derived from the face shell thickness, which can be variable.
Adapted from ASTM C 90. A Average of measurements on three units taken at the thinnest point. B This face-shell thickness is applicable where the allowable design load is reduced in proportion to the reduction in thickness from the basic face-shell thickness shown.
4 Hilti, Inc. (US) 1-800-879-8000 | www.us.hilti.com I en español 1-800-879-5000 I Hilti (Canada) Corp. 1-800-363-4458 I www.hilti.ca I Product Technical Guide 2008
01_Intro_.QXD:H440.06_0102 IntroGenInf.QXD
12/30/07
12:45 AM
Page 5
Fastening Technology
Base Materials 2.1 2.1.3.2 Brick
2.1.3.4 Mortar
Bricks are prismatic masonry units made from suitable mixture of soil, clay and a stabilizing agent (emulsified asphalt). They are shaped by molding, pressing or extruding and are fired at elevated temperature to meet the strength and durability requirements of ASTM C62 for solid brick and C652 for hollow brick.
Mortar is the product which is used in the construction of reinforced and non-reinforced unit masonry structures. The role of mortar when hardened in the finished structure is to transfer the compressive, tensile and shear stresses between the units. Mortar consists of a mixture of cementitious material, aggregate and water combined in accordance with ASTM C270. Either a cement/lime mortar or a masonry mortar, each in four types, can be used under this specification. Mortar
Depending upon the grade, brick (solid clay masonry) can have a compressive strength ranging from 1,250 to over 25,000 psi. 12" Brick Grouted multi-wyte masonry construction Bearing Walls typically consists of two wythes, each one unit masonry in thickness, separated by a space 2” to 4-1/2” in width, which is filled with grout. The wythes are connected with wall ties. This space may also be reinforced with vertical reinforcing bars. Solid brick masonry consists of abutting wythes interlaced with header courses. In general, chemical anchors are recommended for use in brick. In older unreinforced construction (URM), or where the condition of the masonry is unknown, it is advisable to use a screen tube to prevent unrestricted flow of the bonding material into voids.
2.1.3.3 Clay Tile Structural clay load-bearing wall tile is made from clay or shale and heat treated (fired) at an elevated temperature to develop the strength and durability required by ASTM C34. These units are manufactured in a variety of shapes and sizes with one or more cavities and develop a compressive strength of 500 to 1000 psi depending upon the grade and type. These units typically have a 3/4" face shell thickness and 1/2" interior web thickness.
Cement-Lime
Masonry Cement
Type
M S N O M S N O
Average Compressive Strength at 28 Days, Min psi (MPa)
2500 1800 750 350 2500 1800 750 350
(17.2) (12.4) (5.2) (2.4) (17.2) (12.4) (5.2) (2.4)
Since mortar plays a significant role in the structural integrity of the masonry wall, it is important to understand how post installed anchors interact with the structure. Within a masonry structure there are designated joint locations. The proximity of a post-installed anchor or power-actuated fastener to one of these locations must be considered in the design of the anchorage. Product specific guidelines are provided within the guide.
2.1.3.5 Grout ACI defines grout as “a mixture of cementitious material and water, with or without aggregate, proportioned to produce a pourable consistency without segregation of the constituents”. The terms grout and mortar are frequently used interchangeably but are, in actuality, not the same. Grout need not contain aggregate (mortar contains fine aggregate). Grout is supplied in a pourable consistency where mortar is not. Grout fills voids while mortar bonds elements together. Grout is used to fill space or cavities and provide continuity between building elements. In some applications, grout will act in a structural capacity, such as in unreinforced masonry construction.
Clay tile as a base material is somewhat more difficult to anchor to due to the thin face shell and low compressive strength. Adhesive anchors such as the Hilti HIT HY 20 with a wire screen are usually recommended because they spread the load over a larger area and do not produce expansion forces.
Grout, in regards to post-installed anchorages, is specified by the design official. When post-installed anchors are tested for the development of design values, the grout is specified according to applicable ASTM standards. Design engineers are encouraged to become familiar with the characteristics of the grout used in performance testing to better understand the applicability of the design loads published in this guide to the actual jobsite.
Hilti, Inc. (US) 1-800-879-8000 | www.us.hilti.com I en español 1-800-879-5000 I Hilti (Canada) Corp. 1-800-363-4458 I www.hilti.ca I Product Technical Guide 2008 5
01_Intro_.QXD:H440.06_0102 IntroGenInf.QXD
12/30/07
12:45 AM
Page 6
Fastening Technology
2.1 Base Materials 2.1.4 Gypsum Wallboard Gypsum wall board consists of an incombustible core, essentially gypsum, surfaced with paper firmly bonded to the core. It is made in flat sheets 4 feet by 8 feet or larger, and from 1/4" to 5/8" thick in accordance with ASTM C 1396/C 1396M. Gypsum wallboard is attached to the wall studs and ceiling joints in residential and commercial building to form the base for the finished wall or ceiling treatment. Gypsum wall board does not have the capacity to accept high loads. Hilti offers several light duty anchors designed for use in gypsum wallboard.
2.1.5 Light Gauge Steel Framing Light gauge steel framing uses cold-formed steel sections for the construction of walls, floors and roofs. The framing memers have industry standard dimensions similar to wood framing studs. There are a large variety of shapes and sizes available for both residential and commercial markets. Framing members are generally produced in C-sections with thicknesses of 12 to 25 GA and varying widths. Other specialized shapes and connection components are also available from a variety of manufacturers. Design of light gauge steel framing is done in accordance with the American Iron and Steel Institute (AISI) Cold-Formed Steel Design Manual. Powder-actuated fasteners, self-drilling screws and anchors are commonly used in light gauge steel construction. Powderactuated fasteners and anchors are used to attach the light gauge steel to concrete and steel base materials. Self-drilling screws are used to attach light gauge steel components as part of larger assemblies or systems. Fasteners are typically evaluated without the steel elements. The elements should be evaluated separately based on applicable AISI design requirements. In some instances, such as steel deck diaphragms, deflection slip clips and perimeter wall track at edge of slab, powder-actuated fasteners have been tested with the light gauge steel components as a system assembly and the corresponding data is provided in this Product Technical Guide.
2.1.6 Autoclave Aerated Concrete Precast autoclaved aerated concrete (AAC) is a lightweight, precast building material of a uniform porous structure. Adding aluminum powder to a cement, lime, fine sand and water mixture causes it to expand dramatically. After mixing, the slurry is poured into a mold and allowed to “rise”. The product is removed from its mold after a few hours and fed through a cutting machine, which sections the AAC into
predetermined sizes. These AAC products are then placed into an autoclave and steam cured for 10 to 12 hours. Autoclaving initiates a second chemical reaction that transforms the material into a hard calcium silicate. AAC was developed in Europe and is currently being manufactured in the United States by licensed facilities. Strength Class
Average Compressive Strength, psi (N/mm2)
Average Comp. Str. Density lb/ft3 (g/cm3)
AAC - 2 AAC - 4 AAC - 6
360 (2.5) 725 (5.0) 1090 (7.5)
32 (0.5) 38 (0.6) 44 (0.7)
Due to the low compressive strength of AAC, anchors that spread the load over the entire embedded section are preferred (e.g., HUD, HRD, adhesives).
2.1.7 Steel Structural steel is a critical building component which serves as the main structural support in many structures. Iron ore is processed and combined with other elements to produce different types of steel. Reference to a particular type of steel is usually made by ASTM standard. For example, ASTM A36 is the specification for what is usually referred to as A36 steel. Steel is hot-rolled into structural shapes that are available in different grades, with the grade corresponding to the yield strength. Common grades of structural steel include ASTM A36, which has a minimum yield strength of 36 ksi and ASTM A572, which is available in grades 42, 50, 55, 60 and 65. ASTM A992 is a high strength steel used extensively for wide flanged shapes. The grade of steel is very important when selecting a power actuated fastener. The grade and thickness determine the resistance that must be overcome when setting the fastener. The power required to drive a fastener must be greater than the resistance. If the power and resistance are too high, the fastener could be damaged during the setting process. This is referred to as exceeding the application range for the fastener. For a given fastener, the application range is determined by its length, diameter, material strength and hardness.
2.1.8 Pre-tensioned/ Pre-stressed Concrete Pre-tensioned / prestressed concrete is concrete that is cast around already tensioned tendons or strands. This method produces a good bond between the tendon and concrete, which both protects the tendon from corrosion and allows for direct transfer of tension. The cured concrete adheres and bonds to the bars and when the tension is released it is transferred to the concrete as compression by static friction. Most pre-tensioned / prestressed concrete elements are prefabricated in a factory and must be transported to the construction site, which limits their size.
6 Hilti, Inc. (US) 1-800-879-8000 | www.us.hilti.com I en español 1-800-879-5000 I Hilti (Canada) Corp. 1-800-363-4458 I www.hilti.ca I Product Technical Guide 2008
01_Intro_.QXD:H440.06_0102 IntroGenInf.QXD
12/30/07
12:45 AM
Page 7
Fastening Technology
Evaluation of Test Data 2.2 Pre-tensioned / prestressed concrete poses a unique problem when post-installed anchors and power-actuated fasteners are used. Drilling into the concrete is typically not recommended unless a precise knowledge of the location of the tendons is known. Since locating the tendons can be tedious and expensive other alternatives for post-installed anchors are needed. Typically, the clear cover over the tendons is known and can be used to provide connection points. Post-installed anchors and power-actuated fasteners with embedments on the magnitude of 3/4" to 1” are typically ideal and do not interfere with the tendons or strands.
2.1.9 Bonded Post-tensioned Concrete Bonded post-tensioned concrete is a term used for a method of applying compression after pouring concrete and the curing process. This method is commonly used to create monolithic slabs. Slabs are created in-situ versus being manufactured at a plant. The same considerations for avoiding post-tensioning strands should be considered when using post-installed anchors and power-actuated fasteners.
2.1.10 Admixtures Chemical admixtures are the ingredients in concrete other than Portland cement, water and aggregate that are added to the mix immediately before or during mixing. Chemical admixtures are used to enhance the properties of concrete and mortar in the plastic and hardened state. These properties may be modified to increase compressive and flexural strength at all ages, decrease permeability and improve durability, inhibit corrosion, reduce shrinkage, accelerate or retard initial set, increase slump and workability, improve pumpability and finishability, increase cement efficiency, and improve the economy of the mixture. An admixture or combination of admixtures may be the only feasible means of achieving the desired results. Testing of post-installed anchors and power-actuated fasteners is performed in concrete without admixtures. Designers should take into consideration the affects of admixtures to the concrete when determining the applicability of particular post-installed anchors or power-actuated fasteners.
2.2.1 Developing Fastener Performance Data Hilti published data is based on laboratory testing unless otherwise indicated. However, the emergence of accurate predictive methods, as embodied in the Concrete Capacity Design (CCD) method, allows for calculation of anchor capacity for a variety of design conditions. The CCD method is applicable to anchors for which pre-qualification testing has been performed in accordance with the testing standard developed by ACI Committee 355.
Fastener testing at Hilti is conducted in accordance with ASTM E 488, Standard Test Methods for Strength of Anchors in Concrete and Masonry Elements, ASTM E 1512 Standard Test Methods for Testing Bond Performance of Bonded Anchors and ASTM E 1190 Standard Test Methods for Strength of Power-Actuated Fasteners Installed in Structural Members. Because of the wide variation in possible concrete reinforcing configurations found in construction, testing is typically performed in unreinforced concrete, which gives conservative results. There are two methods of developing allowable loads; (1) apply an appropriate safety factor to the mean ultimate load as determined from a given number of individual tests, or (2) apply a statistical method to the test data which relates the allowable working load to the performance variability of the fastening.
2.2.2 Allowable Loads Historically, allowable loads for anchors have been derived by applying a global safety factor to the average ultimate value of test results. This approach is characterized by Eq. 2.2.1. Eq. 2.2.1
Fall =
F v
Where: F = mean of test data (population sample) v = safety factor Global safety factors of 4 to 8 for post-installed anchors have been industry practice for nearly three decades. The global safety factor is assumed to cover expected variations in field installation conditions and variation in anchor performance from laboratory tests. Note that global safety factors applied to the mean do not explicitly account for anchor coefficient of variation, i.e., all anchors are considered equal with respect to variability in the test data.
2.2.3 Statistical Evaluation of Data Experience from a large number of tests on anchors has shown that ultimate loads generally approximate a normal Gaussian probability density function as shown in Fig. 2.2.1. This allows for the use of statistical evaluation techniques that relate the resistance to the system performance variability associated with a particular anchor. One such technique is to adjust the mean such that the resulting resistance represents a so-called 5% fractile, or characteristic value. As commonly applied, the characteristic load, Rk, for a given test series is derived from the mean, F, the standard deviation, s, and the sample size, n, such that, for a 90% probability (90% confidence) 95% of the loads are above
Hilti, Inc. (US) 1-800-879-8000 | www.us.hilti.com I en español 1-800-879-5000 I Hilti (Canada) Corp. 1-800-363-4458 I www.hilti.ca I Product Technical Guide 2008 7
01_Intro_.QXD:H440.06_0102 IntroGenInf.QXD
12/30/07
12:45 AM
Page 8
Fastening Technology
2.2 Evaluation of Test Data
Wahrscheinlichkeitsdichte Probability density
Frequency Häufigkeit [%] (%)
the characteristic load. The characteristic load is calculated according to Eq. 2.2.2 whereby k is usually provided by a onesided population limit for a standard distribution for sample size n. Histogram of the Histogramm der Versuchsergebnisse test results
Probability density Wahrscheinlichkeitsdichte
R Rkk
FFrec ALL Frec Rk F ALL==Rk/ν
on the characteristic resistance. Unless stated otherwise, the following safety factors are applied to the characteristic resistance: v
=
3 for concrete and bond failure modes
v
=
5 for shallow anchors (due to the greater variability associated with cover concrete) and plastic anchors
These safety factors are intended to cover the following conditions, within reasonably expected variations: Ru,m F
Versagenslast Ultimate Load
v
Fig. 2.2.1 Frequency distribution of fastener loads, demonstrating the significance of the 5% fractile and the allowable load As applied to the characteristic resistance, the global safety factor, v, is not required to account for the variability of the system. This allows for a tighter definition of the components to be covered by the safety factor, such as concrete variability and the variability of lab test data with respect to field performance. (Taken together with an ultimate strength design method, whereby loading variability is accommodated via load factors, the partial safety factors associated with these effects can be converted into a strength reduction factor, f, thus allowing for greater consistency in the safety factor). Fastening systems exhibiting tightly grouped test data are rewarded with a low standard deviation, s.
1. variability of anchor performance in the field with respect to laboratory performance 2. variability of actual loading with respect to calculated loads 3. typical variability of base material (e.g., concrete) condition with respect to specified or laboratory conditions 4. reasonable installation deviations Note that installation error, e.g., installation not in accordance with Hilti’s installation instructions, is not covered by the safety factor. It is the responsibility of the user or design engineer to examine all factors that could influence an anchorage and to adjust the design resistance accordingly.
Fall = Rk = F - k · s = F (1 - k · cv) v v v
Eq. 2.2.2 Where: Rk
=
characteristic resistance of the tested anchor system
F
=
mean ultimate resistance of the tested anchor system
k
=
distribution value for test sample size n
s
=
standard deviation of the test data
cv
=
coefficient of variation = s F
v
=
safety factor
Many of the allowable loads in this Technical Guide are based
8 Hilti, Inc. (US) 1-800-879-8000 | www.us.hilti.com I en español 1-800-879-5000 I Hilti (Canada) Corp. 1-800-363-4458 I www.hilti.ca I Product Technical Guide 2008
01_Intro_.QXD:H440.06_0102 IntroGenInf.QXD
12/30/07
12:45 AM
Page 9
Fastening Technology
Corrosion 2.3 2.3.1 The Corrosion Process
Galvanic Series of Metals and Alloys
Corrosion is defined as the chemical or electrochemical reaction between a material, usually a metal, and its environment that produces a deterioration of the material and its properties (ASTM G 15). The corrosion process can be very complex and have many contributing factors that lead to immediate or delayed destructive results. In anchorage and fastener design, the most common types of corrosion are direct chemical attack and electro-chemical contact.
Corroded End (anodic, or least noble) Magnesium Magnesium alloys Zinc Aluminum 1100 Cadmium Aluminum 2024-T4 Steel or Iron Cast Iron Chromium-iron (active) Ni-Resist cast iron Type 304 Stainless (active) Type 316 Stainless (active) Lead tin solders Lead Tin Nickel (active) Inconel nickel-chromium alloy (active) Hastelloy Alloy C (active) Brasses Copper Bronzes Copper-nickel alloys Monel nickel-copper alloy Silver solder Nickel (passive) Inconel nickel-chromium alloy (passive) Chromium-iron (passive) Type 304 Stainless (passive) Type 316 Stainless (passive) Hastelloy Alloy C (passive) Silver Titanium Graphite Gold Platinum Protected End (cathodic, or most noble)
2.3.2 Types of Corrosion 2.3.2.1 Direct Chemical Attack Corrosion by direct chemical attack occurs when the base material is soluble in the corroding medium. One method of mitigating these effects is to select a fastener that is not susceptible to attack by the corroding chemical. Compatibility tables of various chemical compounds with Hilti adhesive and epoxy fastening systems are provided in this Product Technical Guide. When selection of a base metal compatible with the corroding medium is not possible or economical, another solution is to provide a coating that is resistant to the corroding medium. These might include metallic coatings such as zinc or organic coatings such as epoxies or fluorocarbons.
2.3.2.2 Electrochemical Contact Corrosion All metals have an electrical potential relative to each other and have been ranked accordingly to form the “electromotive force series” or galvanic series of metals. When metals of different potential come into contact in the presence of an electrolyte (moisture), the more active metal with more negative potential becomes the anode and corrodes, while the other metal becomes the cathode and is galvanically protected. The severity and rate of attack will be influenced by: a. Relative position of the contacting metals in the galvanic series, b. Relative surface areas of the contacting materials and, c. Conductivity of the electrolyte. The effects of electro-chemical contact corrosion may be mitigated by: a. Using similar metals close together in the electromotive force series,
Source: IFI Fastener Standards, 6th Edition
b. Separating dissimilar metals with gaskets, plastic washers or paint with low electrical conductivity. Materials typically used in these applications include: 1. High Density Polyethylene (HDPE) 2. Polytetrafluoroethylene (PTFE) 3. Polycarbonates 4. Neoprene / chloroprene 5. Cold galvanizing compound 6. Bituminous coatings or paint Note: Specifiers must ensure that these materials are compatible with other anchorage components in the service environment. c. Selecting materials so that the fastener is the cathode, most noble or protected component, d. Providing drainage or weep holes to prevent entrapment of the electrolyte
Hilti, Inc. (US) 1-800-879-8000 | www.us.hilti.com I en español 1-800-879-5000 I Hilti (Canada) Corp. 1-800-363-4458 I www.hilti.ca I Product Technical Guide 2008 9
01_Intro_.QXD:H440.06_0102 IntroGenInf.QXD
12/30/07
12:45 AM
Page 10
Fastening Technology
2.3 Corrosion 2.3.2.3 Hydrogen Assisted Stress Corrosion Cracking Often incorrectly referred to as hydrogen embrittlement, hydrogen assisted stress corrosion cracking (HASCC) is an environmentally induced failure mechanism that is sometimes delayed and most times occurs without warning. HASCC occurs when a hardened steel fastener is stressed (loaded) in a service environment which chemically generates hydrogen (such as when zinc and iron combine in the presence of moisture). The potential for HASCC is directly related to steel hardness. The higher the fastener hardness, the greater the susceptibility to stress corrosion cracking failures. Eliminating or reducing any one of these contributing factors (high steel hardness, corrosion or stress) reduces the overall potential for this type of fastener failure. Hydrogen embrittlement, on the other hand, refers to a potential damaging side effect of the steel fastener manufacturing process, and is unrelated to project site corrosion. Hydrogen embrittlement is neutralized by proper processing during fastener pickling, cleaning and plating operations, specifically by “baking” the fasteners after the application of the galvanic coating.
2.3.3 Corrosion Protection The most common material used for corrosion protection of carbon steel fasteners is zinc. Zinc coatings can be uniformly applied by a variety of methods to achieve a wide range of coating thickness depending on the application. All things being equal, thicker coatings typically provide higher levels of protection. An estimating table for the mean corrosion rate and service life of zinc coatings in various atmospheres is provided to the right. These values are for reference only, due to the large variances in the research findings and specific project site conditions, but they can provide the specifier with a better understanding of the expected service life of zinc coatings. In controlled environments where the relative humidity is low and no corrosive elements are present, the rate of corrosion of zinc coatings is approximately 0.15 microns per year.
Atmosphere
Mean Corrosion Rate
Industrial Urban Non-Industrial or Marine Suburban Rural Indoors
5.6 µm/year 1.5 µm/year 1.3 µm/year 0.8 µm/year Considerably less than 0.5 µm/year
Source: ASTM B 633 Appendix X1. Service Life of Zinc
2.3.3.1 Suggested Corrosion Resistance Use of AISI 316 stainless steel in environments where pitting or stress corrosion is likely should be avoided due to the possibility of sudden failure without visual warning. Fastenings in these applications should be regularly inspected for serviceability condition. See chart 2.3.3.1 below.
Corrosion Resistance
Typical Conditions of Use
Phosphate and Oil Coatings (Black Oxide)
• Interior applications without any particular influence of moisture
Zinc electro-plated 5 – 10 µm • Interior applications without any (ASTM B 633, SC 1, Type III) particular influence of moisture Organic Coatings – • If covered sufficiently by Kwik Cote ≥ 17.8 µm noncorrosive concrete Mechanically deposited zinc coating 40 – 107 µm Hot-Dip Galvanizing (HDG) > 50 µm (ASTM A 153)
• Interior applications in damp environments and near saltwater (ASTM B 695) • Exterior applications in only slightly corrosive atmospheres
Sherardizing Process > 50 µm Stainless Steel (AISI 303 / 304)
• Interior applications where heavy condensation is present • Exterior applications in corrosive environments
Stainless Steel (AISI 316)
• Near saltwater • Exterior corrosive environments
Zinc coatings can be applied to anchors and fasteners by different methods. These include (in order of increasing coating thickness and corrosion protection): a. ASTM B 633 – Standard Specification for Electrodeposited Coatings of Zinc on Iron and Steel b. ASTM B 695 – Standard Specification for Coatings of Zinc Mechanically Deposited on Iron and Steel c. ASTM A 153 – Standard Specification for Zinc Coating (Hot-Dip) on Iron and Steel Hardware d. Sherardizing Process – Proprietary Diffusion Controlled Zinc Coating Process
10 Hilti, Inc. (US) 1-800-879-8000 | www.us.hilti.com I en español 1-800-879-5000 I Hilti (Canada) Corp. 1-800-363-4458 I www.hilti.ca I Product Technical Guide 2008
01_Intro_.QXD:H440.06_0102 IntroGenInf.QXD
12/30/07
12:45 AM
Page 11
Fastening Technology
Corrosion 2.3 2.3.4 Test Methods Various test methods have been used in the development of Hilti fastening systems to predict performance in corrosive environments. Some of the internationally accepted standards and test methods used in these evaluations are: a. ASTM B 117 Standard Practice for Operating Salt Spray (Fog) Apparatus b. ASTM G 85 Standard Practice for Modified Salt Spray (Fog) Testing c. ASTM G 87 Standard Practice for Conducting Moist SO2 Tests d. DIN 50021 – SS Salt Spray Testing (ISO 3768) e. DIN 50018 2,0 Kesternich Test (ISO 6988) Testing in a Saturated Atmosphere in the Presence of Sulfur Dioxide
2.3.5 Hilti Fastening Systems 2.3.5.1 Anchors Most Hilti metal anchors are available in carbon steel with an electrodeposited zinc coating of at least 5 µm with chromate passivation. Chromate passivation reduces the rate of corrosion for zinc coatings, maintains color, abrasion resistance and when damaged, exhibits a unique “self healing” property. This means that the chromium contained within the film on the anchor surface will repassivate any exposed areas and lower the corrosion rate. Hilti standard and super HAS threaded rods in 7/8" diameter size are zinc coated to at least 50 µm by the hot-dip galvanizing process. Other sizes may be available through special orders. Where the long-term integrity of a fastening is important, and there is a risk of corrosion of a carbon steel anchor, then a stainless steel anchor may be specified. It must be noted that under certain extreme conditions, even stainless steel anchors will corrode and additional protective measures will be needed. Stainless steels should not be used when the anchorage will be subjected to long term exposure, immersion in chloride solutions, or in corrosive environments where the average temperature is above 86° F. Hilti HCR High Corrosion Resistant threaded rod is available on a special order basis. It provides superior corrosion resistance to AISI 316 and is an alternative to titanium or other special stainless steels.
2.3.5.2 Power-Actuated Fasteners Hilti carbon steel power-actuated fasteners are typically zinc plated to a minimum thickness of 5 µm for limited corrosion resistance. Another method used to resist corrosion for the Hilti carbon steel ENP series decking fasteners is the use of the stainless steel SDK2 sealing cap with an integrated neoprene seal. Please see Section 3.4.1.3.1. Hilti also manufactures stainless steel X-CR powder-actuated nails and threaded studs. The X-CR fasteners are made from a proprietary material with corrosion resistance equivalent to AISI 316 material, but with higher strength and hardness. Because carbon steel power-actuated fasteners are hardened, they can be susceptible to HASCC. It is, therefore, important to evaluate the suitability of the application prior to use if the environment may be corrosive. If in doubt, stainless steel X-CR fasteners are recommended.
2.3.5.3 Screw Fasteners Hilti screw fasteners are available with three different types of coatings: a. phosphate and oil (black oxide) b. zinc electroplated c. Kwik-Cote Black oxide offers the lowest resistance to corrosion and generally restricts use to interior finishing applications. Hilti Kwik-Cote is a proprietary copolymer organic coating that helps protect against galvanic corrosion in a manner similar to zinc. Zinc electro-plating is in accordance with ASTM B 633 SC 1 Type III to a minimum thickness of 5 µm. Hilti provides the proprietary Kwik-Cote organic coating on certain types of Kwik-Pro screws and all Kwik-Flex screws. Stainless steel screws (AISI 410 or 300 series) and sealing washers are available on a special order basis. Warning: Because of the potential for HASCC failures, standard hardened carbon steel fasteners are not recommended for use with dissimilar metals or chemically treated wood when moisture may be present or in corrosive environments. For screws that are resistant to HASCC, consider using Hilti Kwik-Flex screws.
Note: Specifiers should also consult ACI 318-05 Chapter 4 Durability Requirements, Section 4.4 and Tables 4.4.1 and 4.2.2 for applications where concrete structures will be exposed to chloride ion concentrations, deicing chemicals, salt, salt water, brackish water, seawater or spray from these sources.
Hilti, Inc. (US) 1-800-879-8000 | www.us.hilti.com I en español 1-800-879-5000 I Hilti (Canada) Corp. 1-800-363-4458 I www.hilti.ca I Product Technical Guide 2008 11
01_Intro_.QXD:H440.06_0102 IntroGenInf.QXD
12/30/07
12:45 AM
Page 12
Fastening Technology
2.3 Corrosion 2.3.6 Applications It is difficult to offer generalized solutions to corrosion problems. An applications guide can be useful as a starting point for fastener material selection. The specifier should also consult: a. Local and national building code requirements (e.g., IBC, UBC) b. Standard practice manuals for specific types of construction (e.g., ACI, PCI, AISC, PCA, CRSI, AASHTO, NDS/APA) c. Manufacturers of structural components d. Hilti technical support
2.3.6.1 General Applications8 Application
Conditions
Fastener Recommendations
Structural steel components to concrete & masonry (interior connections within the building envelope not subjected to free weathering) 1, 2
Interior applications without condensation
Galvanic zinc plating
Interior applications with occasional condensation
HDG or Sherardized
Structural steel components to concrete & masonry (exterior connections subjected to free weathering) 1,2
Slightly corrosive environments
HDG or Sherardized
Highly corrosive environments
Stainless steel
Zinc coated or painted metal decking to steel beam / joist connections with roof membrane or cover 3, 4, 5
Interior applications without condensation
Galvanic zinc plating or Kwik-Cote
Exposed deck applications subject to free weathering 3, 4, 5
With sealing washers (SDK2)
Galvanic zinc plating
Without sealing washers (SDK2)
X-CR
Composite deck applications (steel connections with concrete overlayment) 1
Covered sufficiently by non-corrosive concrete
Galvanic zinc plating
Insulation fastenings / EIFS fastenings 6
Applications without condensation
Galvanic zinc plating or Kwik-Cote
Applications with condensation
X-CR
Interior applications
Galvanic zinc plating
Exterior applications
HDG or Sherardized
Parking garages / parking decks subject to periodic application of de-icers including chloride solutions 7
Non-safety critical
HDG, Sherardized or X-CR1
Safety critical
Stainless steel1
Road / bridge decks subject to periodic application of de-icers including chloride solutions
Non-safety critical
HDG or Sherardized
Safety critical
Stainless steel
Temporary formwork, erection bracing and short-term scaffolding
1 2 3 4 5 6 7 8
Refer to ACI 318 Chapter 4 – Durability Refer to ACI 530.1 Section 2.4F – Coatings for Corrosion Protection Refer to SDI “A Rational Approach to Steel Deck Corrosion Protection” Refer to Factory Mutual Approval Standard Class No. 4450 Section 5.4 Refer to Factory Mutual Approval Standard Class No. 4470 Section 5.6 Refer to ICC Evaluation Services Acceptance Criteria 24 – Exterior Insulation and Finish Systems Refer to PCI Parking Structures: Recommended Practice for Design & Construction – Chapters 3, 5 and Appendix General guidelines address environmental corrosion (direct chemical attack). Additional considerations should be taken into account when using hardened steel fasteners susceptible to HASCC.
12 Hilti, Inc. (US) 1-800-879-8000 | www.us.hilti.com I en español 1-800-879-5000 I Hilti (Canada) Corp. 1-800-363-4458 I www.hilti.ca I Product Technical Guide 2008
01_Intro_.QXD:H440.06_0102 IntroGenInf.QXD
12/30/07
12:45 AM
Page 13
Fastening Technology
Corrosion 2.3 2.3.6.2 Special Applications These application charts are offered as general guidelines.4 Site specific conditions may influence the decision. Application
Conditions
Fastener Recommendations
Aluminum fastenings (flashing / roofing accessories, hand rails, grating panels, sign posts and miscellaneous fixtures)
Interior applications without condensation
Galvanic zinc plating or Kwik-Cote
Exterior applications with condensation
Stainless steel, X-CR
Not submerged
HDG, Sherardized or Stainless steel
Submerged
Stainless steel 2
Not submerged
HDG, Sherardized or Stainless steel
Submerged
Stainless steel 2
Non-safety critical or temporary connections
HDG, Sherardized or X-CR
High humidity with the presence of chlorides – splash zone
Stainless steel1
On the off-shore platform or rig
Stainless steel or X-CR
Non-safety critical
HDG or Sherardized, X-CR
Safety critical or subjected to high concentrations of soluble chlorides
Stainless steel1
Above grade
HDG
Below grade
Stainless steel, X-CR
Non-safety critical
HDG or Stainless steel
Safety critical or subjected to high concentrations of SO2
Stainless steel, X-CR1
Non-safety critical
HDG, Stainless steel or X-CR
Safety critical
Stainless steel1
Water treatment
Waste water treatment
Marine (salt water environments, shipyards, docks, off-shore platforms)
Indoor swimming pools
Pressure / chemically treated wood 3
Power plant stacks / chimneys
Tunnels (lighting fixtures, rails, guardposts)
1 2 3 4
Steel selection depends on safety relevance Must electrically isolate fastener from contact with concrete reinforcement through use of adhesive or epoxy anchoring system, gasket or plastic washer with low electrical conductivity Refer to APA Technical Note No. D485D and AF & PA Technical Report No. 7 General guidelines address environmental corrosion (direct chemical attack). Additional considerations should be taken into account when using hardened steel fasteners susceptible to HASCC.
Hilti, Inc. (US) 1-800-879-8000 | www.us.hilti.com I en español 1-800-879-5000 I Hilti (Canada) Corp. 1-800-363-4458 I www.hilti.ca I Product Technical Guide 2008 13
01_Intro_.QXD:H440.06_0102 IntroGenInf.QXD
12/30/07
12:45 AM
Page 14
Fastening Technology
Notes
14 Hilti, Inc. (US) 1-800-879-8000 | www.us.hilti.com I en español 1-800-879-5000 I Hilti (Canada) Corp. 1-800-363-4458 I www.hilti.ca I Product Technical Guide 2008
01_Intro_.QXD:H440.06_0102 IntroGenInf.QXD
12/30/07
12:45 AM
Page 15
Fastening Technology
Notes
Hilti, Inc. (US) 1-800-879-8000 | www.us.hilti.com I en español 1-800-879-5000 I Hilti (Canada) Corp. 1-800-363-4458 I www.hilti.ca I Product Technical Guide 2008 15
01_Intro_.QXD:H440.06_0102 IntroGenInf.QXD
12/30/07
12:45 AM
Page 16
Direct Fastening Systems
Direct Fastening Systems Table of Contents Section
Description
3.1 3.1.1 3.1.2 3.1.3
Direct Fastening Terminology & Applications . . . . . . . . . . . . . . . . . . . . . . . . . . . . . . . . . . . 18 Direct Fastening Terminology . . . . . . . . . . . . . . . . . . . . . . . . . . . . . . . . . . . . . . . . . . . . . . . . . . 18 Benefits of Direct Fastening systems . . . . . . . . . . . . . . . . . . . . . . . . . . . . . . . . . . . . . . . . . . . . 19 Common Direct Fastening Applications . . . . . . . . . . . . . . . . . . . . . . . . . . . . . . . . . . . . . . . . . . 19
3.2 3.2.1 3.2.1.1 3.2.1.2 3.2.1.3
General Construction Fastening Systems . . . . . . . . . . . . . . . . . . . . . . . . . . . . . . . . . . . . . . 20 General Construction Fastener Design & Selection . . . . . . . . . . . . . . . . . . . . . . . . . . . . . . . . . 20 Fastening to Concrete . . . . . . . . . . . . . . . . . . . . . . . . . . . . . . . . . . . . . . . . . . . . . . . . . . . . . . . 20 Fastening to Steel . . . . . . . . . . . . . . . . . . . . . . . . . . . . . . . . . . . . . . . . . . . . . . . . . . . . . . . . . . . 24 Fastener Selection Guide . . . . . . . . . . . . . . . . . . . . . . . . . . . . . . . . . . . . . . . . . . . . . . . . . . . . . 27
3.2.2
Page
General Application Fasteners . . . . . . . . . . . . . . . . . . . . . . . . . . . . . . . . . . . . . . . . . . . . . . . . . 31 X-U, DS, EDS, X-ZF, X-S13, X-DAK, X-DNI, X-EDNI, X-GN, X-EGN and X-GHP fastener series for general applications to concrete, steel or masonry
3.2.3
X-U Universal Knurled Shank Fastener . . . . . . . . . . . . . . . . . . . . . . . . . . . . . . . . . . . . . . . . . . 37 Universal X-U fastener for use in concrete, steel or masonry
3.2.4
Perimeter Wall Application Fasteners . . . . . . . . . . . . . . . . . . . . . . . . . . . . . . . . . . . . . . . . . . . . 40 X-U, DS and EDS fasteners for attachment of perimeter track and deflection slip clips to concrete or steel
3.2.5
Drywall Track Fastening Systems . . . . . . . . . . . . . . . . . . . . . . . . . . . . . . . . . . . . . . . . . . . . . . . 45 X-S13, X-DAK, X-DW, X-S16, X-GN, X-EGN, and X-GHP fastener series for attachment of drywall track to concrete, steel or masonry
3.2.6
Sill Plate Fastening Systems . . . . . . . . . . . . . . . . . . . . . . . . . . . . . . . . . . . . . . . . . . . . . . . . . . 49 X-CF 72, X-ZF 72, X-DNI 72, X-CP 72, and X-CR-L 72 fasteners for attachment of wood sill plates to concrete
3.2.7
Ceiling Clip & Hanger Assemblies . . . . . . . . . . . . . . . . . . . . . . . . . . . . . . . . . . . . . . . . . . . . . . 51 Sheet steel clips with pre-mounted powder-actuated fasteners with or without pre-tied wire for suspending acoustical ceiling grids and panels from concrete
3.2.8
Stud Fasteners for Attachment to Concrete . . . . . . . . . . . . . . . . . . . . . . . . . . . . . . . . . . . . . . 53 Carbon steel (1/4” and 3/8”) and stainless steel (1/4”) powder-actuated threaded studs for attachment to concrete
3.2.9
Stud Fasteners for Attachment to Steel . . . . . . . . . . . . . . . . . . . . . . . . . . . . . . . . . . . . . . . . . . 56 Carbon steel (1/4”, 3/8” and 8mm) and stainless steel (3/8” and 8mm) powder-actuated threaded studs for attachment to steel
3.2.10
.
X-BT Fastening Systems . . . . . . . . . . . . . . . . . . . . . . . . . . . . . . . . . . . . . . . . . . . . . . . . . . . . . 59 Innovative X-BT (3/8” and 8mm) blunt-tip threaded stud fastener for attachment to coated or painted steel
3.2.11
Clips & Hangers for Mechanical and Electrical Applications . . . . . . . . . . . . . . . . . . . . . . . . . . 64 Threaded and smooth rod hangers (X-HS and X-RH), cable holders, clamps and tie fasteners (X-ECH, X-EKB MX, and X-ECT) and conduit clips (X-BX, X-EMTC and X-EMTSC MX) for use in miscellaneous mechanical and electrical applications
3.2.12
Insulation or Soft Material Attachment Fasteners . . . . . . . . . . . . . . . . . . . . . . . . . . . . . . . . . . 69 X-IE and X-SW fasteners for attachment of insulation and other soft materials to concrete, masonry or steel
16 Hilti, Inc. (US) 1-800-879-8000 | www.us.hilti.com I en español 1-800-879-5000 I Hilti (Canada) Corp. 1-800-363-4458 I www.hilti.ca I Product Technical Guide 2008
02_3.0_DX_Mod15.QXD:H440.04_03 DX.QXD
12/30/07
12:49 AM
Page 17
Direct Fastening Systems
Direct Fastening Systems Table of Contents Section
Description
3.3 3.3.1
Grating & Checkerplate Fastening Systems . . . . . . . . . . . . . . . . . . . . . . . . . . . . . . . . . . . . 71 Grating & Checkerplate Fastener Selection . . . . . . . . . . . . . . . . . . . . . . . . . . . . . . . . . . . . . . . 71
3.3.2
Page
X-FCM & X-FCP Grating & Checkerplate Fastening Systems . . . . . . . . . . . . . . . . . . . . . . . . . 72 Removable and reusable grating (X-FCM) & checkerplate (X-FCP) fastening systems available in zinc plated, HDG, and stainless steel corrosion resistance and consisting of a disk that threads onto a powder-actuated threaded stud. Stainless steel version specifically designed for off-shore
3.3.3
X-GR, X-GR RU, & X-MGR Grating Fastening Systems . . . . . . . . . . . . . . . . . . . . . . . . . . . . . 77 Permanent (X-GR), or removable (X-GR RU and X-MGR) grating fastening systems with HDG equivalent corrosion resistance for attachment of grating in on-shore industrial applications
3.4 3.4.1 3.4.1.1 3.4.1.2 3.4.1.3 3.4.1.4 3.4.1.5 3.4.1.6 3.4.1.7 3.4.2
Steel Deck Fastening Systems . . . . . . . . . . . . . . . . . . . . . . . . . . . . . . . . . . . . . . . . . . . . . . . 82 Steel Deck Fastener Design & Selection . . . . . . . . . . . . . . . . . . . . . . . . . . . . . . . . . . . . . . . . . 82 Steel Deck Terminology & Definitions . . . . . . . . . . . . . . . . . . . . . . . . . . . . . . . . . . . . . . . . . . . . 82 Steel Deck Diaphragm Design & Theory . . . . . . . . . . . . . . . . . . . . . . . . . . . . . . . . . . . . . . . . . 84 Fastener, Tool & Cartridge Selection Guide . . . . . . . . . . . . . . . . . . . . . . . . . . . . . . . . . . . . . . . 90 Submittal Information for Roof Deck . . . . . . . . . . . . . . . . . . . . . . . . . . . . . . . . . . . . . . . . . . . . 94 Submittal Information for Floor Deck . . . . . . . . . . . . . . . . . . . . . . . . . . . . . . . . . . . . . . . . . . . . 95 Fastener Quantity Estimation Table . . . . . . . . . . . . . . . . . . . . . . . . . . . . . . . . . . . . . . . . . . . . . 96 Common Steel Deck Dimensions . . . . . . . . . . . . . . . . . . . . . . . . . . . . . . . . . . . . . . . . . . . . . . . 96 Deck Fasteners for Attachment to Bar Joist . . . . . . . . . . . . . . . . . . . . . . . . . . . . . . . . . . . . . . 97 X-EDN19 and X-EDNK22 fasteners for attachment of many types of steel deck to bar joist up to 3/8-inch thick
3.4.3
Deck Fasteners for Attachment to Structural Steel . . . . . . . . . . . . . . . . . . . . . . . . . . . . . . . . 103 X-ENP-19 fastener for attachment of many types of steel deck to structural steel greater than or equal to 1/4-inch thick
3.4.4
X-HVB Shear Connector . . . . . . . . . . . . . . . . . . . . . . . . . . . . . . . . . . . . . . . . . . . . . . . . . . . . . 109 Mechanically attached X-HVB shear connector for use in composite beam construction with steel beams and concrete slabs
3.5 3.5.1 3.5.1.1 3.5.1.2 3.5.1.3 3.5.1.4 3.5.1.5 3.5.2
Screw Fastening Systems . . . . . . . . . . . . . . . . . . . . . . . . . . . . . . . . . . . . . . . . . . . . . . . . . . 112 Self-Drilling Screw Fastener Selection and Design . . . . . . . . . . . . . . . . . . . . . . . . . . . . . . . . 112 Drill Point Selection . . . . . . . . . . . . . . . . . . . . . . . . . . . . . . . . . . . . . . . . . . . . . . . . . . . . . . . . 112 Thread Selection . . . . . . . . . . . . . . . . . . . . . . . . . . . . . . . . . . . . . . . . . . . . . . . . . . . . . . . . . . . 113 Head Style Selection . . . . . . . . . . . . . . . . . . . . . . . . . . . . . . . . . . . . . . . . . . . . . . . . . . . . . . . 114 Sealing Criteria . . . . . . . . . . . . . . . . . . . . . . . . . . . . . . . . . . . . . . . . . . . . . . . . . . . . . . . . . . . . 114 Length Selection . . . . . . . . . . . . . . . . . . . . . . . . . . . . . . . . . . . . . . . . . . . . . . . . . . . . . . . . . . . 114 Kwik-Pro Self-Drilling Screws . . . . . . . . . . . . . . . . . . . . . . . . . . . . . . . . . . . . . . . . . . . . . . . . . 115 Self-drilling screws available in a variety of head styles, thread lengths and drill-flute lengths for screw diameters #6 through 1/4” meeting ASTM C 1513 and SAE J78 or ASTM C954
3.5.3
Kwik-Flex Self-Drilling Screws . . . . . . . . . . . . . . . . . . . . . . . . . . . . . . . . . . . . . . . . . . . . . . . . 123 Self-drilling screws specifically designed to resist embrittlement that can be caused by stress, dissimilar metals and moisture available in HWH head style and diameters #10 through 5/16”
Hilti, Inc. (US) 1-800-879-8000 | www.us.hilti.com I en español 1-800-879-5000 I Hilti (Canada) Corp. 1-800-363-4458 I www.hilti.ca I Product Technical Guide 2008 17
02_3.0_DX_Mod15.QXD:H440.04_03 DX.QXD
12/30/07
12:49 AM
Page 18
Direct Fastening Systems
3.1 Direct Fastening Terminology & Applications 3.1.1 Direct Fastening Terminology DX = Hilti Powder-Actuated Direct Fastening System
Steel Deck Fastening Systems1
GX = Gas-Actuated Fastening Systems
tf
= flange thickness of beam or bar joist for steel decking applications, in. (mm)
Characteristics of Steel and Other Metals = specified minimum ultimate tensile strength of metals, ksi (MPa)
F
= diaphragm flexibility factor, in./lb (mm x 10-6/N)
G'
= diaphragm shear stiffness lb/in. (N/mm x 10-6)
= specified minimum yield strength of metals, ksi (MPa)
q
= allowable diaphragm shear, plf (N/mm)
Characteristics of Concrete and Masonry
Qf
= fastener strength, panel to frame, lb (kN)
fc
= concrete compressive strength as measured by testing of cylinder, psi (MPa)
Sf
= fastener flexibility factor, panel to frame, in./kip (mm/kN)
f'c
= specified concrete compressive strength, psi (MPa)
X-HVB Shear Connector
Fu
Fy
Fastening Details
hr
= nominal rib height, in. (mm)
cmin = minimum edge distance, in. (mm)
Hs
= connector height, in. (mm)
dnom = nominal fastener shank diameter, in. (mm)
Nr
= number of connectors in one rib
D
q
= allowable shear strength, lb (kN)
Qn
= nominal shear strength, lb (kN)
Rg
= coefficient to account for group effect
Rp
= position effect factor shear connectors
wr
= average width of rib, in. (mm)
= thread diameter for threaded studs, in. (mm)
hET = penetration of the fastener point below the surface of the base material, in. (mm) hNVS = nailhead stand-off above the surface fastened into. For nails, this is the surface of the fastened material. For threaded studs, the surface of the base material, in. (mm) Ls
= length of fastener, in. (mm)
Ycon = distance from top of steel beam to top of concrete slab, in. (mm)
smin = minimum fastener spacing, in. (mm)
Screw Fastening Systems 2
tI
= thickness of the fastened material, in. (mm)
L
= total thickness of the fastened material, where more than one layer fastened, in. (mm)
MT = maximum thickness of all attachments to be fastened, including the base material, in. (mm)
= thickness of the base material, in. (mm)
Pss = nominal shear strength (resistance) of screw, lb (kN)
ΣtI tII
Tmax = maximum tightening torque, ft-lb (Nm)
= length of screw, in. (mm)
Pts = nominal tension strength (resistance) of screw, lb (kN)
1 More detailed definitions for Steel Deck Fastening Systems can be found on page 82. 2 Terminology for screw fastener head styles (e.g. hex washer head (HWH)) can be found on page 114.
Fastener Nomenclature1 Fastener Series1
Washer Type2 and Diameter (mm)
X-U 37 P8 MX
Stud Nomenclature1
1. The fastener name preceded by an “E” (e.g. X-EDNI 16 P8), indicates a knurled shank for improved holding Indicates in steel. (Note: X-U fasteners have Collated Fastener knurling.) (strips of 10)
Shank Length (mm)
2. P = Plastic washer Thread Size S = Steel washer (mm) D = Double washer (1 plastic, 1 steel) L = Double washer (both steel) DP = Double washer (both plastic) FP = Ferrule and plastic guide washer
Shank Diameter
Washer Type2 and Diameter (mm)
X-W6 20 22 FP8
3. “MX” at the end of fastener name indicates fasteners collated in strips of 10
Washer
Thread Length (mm)
Shank Diameter
Washer
Shank Length (mm)
Thread Length
Thread Size
18 Hilti, Inc. (US) 1-800-879-8000 | www.us.hilti.com I en español 1-800-879-5000 I Hilti (Canada) Corp. 1-800-363-4458 I www.hilti.ca I Product Technical Guide 2008
02_3.0_DX_Mod15.QXD:H440.04_03 DX.QXD
12/30/07
12:49 AM
Page 19
Direct Fastening Systems
Direct Fastening Terminology & Applications 3.1 3.1.2 Benefits of Direct Fastening Systems Power-actuated fastening systems are recognized as a safe, acceptable and cost effective method of making instantaneous fastenings into various construction base materials such as concrete, steel and masonry. Poweractuated fastening technology uses either powder cartridges (blank cartridges) or compressed gas cartridges. Without the need for external power sources, it is portable, fast and lightweight allowing for reliable fastenings in difficult access areas on today’s construction sites.
Screw fastening systems are commonly used for the attachment of cold-formed steel members. Self-drilling screws allow for direct attachment without the need for additional equipment such as a drill bit or welding machine making screw fastening portable, fast and lightweight. A key benefit to using direct fastening systems is increased productivity for the end user due to the speed of making fastenings vs. drilling and anchoring or welding. Fastenings are easily inspected and suitable for all trades in a variety of applications.
3.1.3 Common Direct Fastening Applications General Fastenings to Concrete
General Fastenings to Steel
Reference Sections 3.2.2, 3.2.3 and 3.2.8
Reference Sections 3.2.2, 3.2.3 and 3.2.9
Interior Partition Walls (Drywall)
Wood Sill Plate Attachment
Ceiling Hangers
Reference Section 3.2.5
Reference Section 3.2.6
Reference Section 3.2.7
Electrical Grounding
Pipe Hangers
Cable & Conduit Attachment
Reference Section 3.2.10
Reference Section 3.2.11
Reference Section 3.2.11
Thermal Insulation Attachment
Grating & Checkerplate Attachment
Reference Section 3.2.12
Reference Section 3.3
Steel Deck Sidelap Attachment
Light Steel Framing Connections
Reference Sections 3.4 and 3.5
Perimeter Wall Applications - Deflection Slip Clips - Steel Framing Track Reference Section 3.2.4
Steel Deck Attachment Reference Section 3.4
Reference Section 3.5
Hilti, Inc. (US) 1-800-879-8000 | www.us.hilti.com I en español 1-800-879-5000 I Hilti (Canada) Corp. 1-800-363-4458 I www.hilti.ca I Product Technical Guide 2008 19
02_3.0_DX_Mod15.QXD:H440.04_03 DX.QXD
12/30/07
12:49 AM
Page 20
General Construction Fastening Systems
3.2.1 General Construction Fastener Design & Selection 3.2.1.1 Fastening to Concrete 3.2.1.1.1 General Suitability A fastener driven into concrete is influenced by the following factors:
When a powder or gas-actuated fastener is driven into concrete, the concrete around the fastener shank is displaced. This displaced concrete compresses against the shank creating a friction hold. In addition, heat generated during the driving process causes a sintering of the concrete to the fastener.
•
Depth of penetration
•
Compressive strength of the concrete
•
Fastener spacing and edge distance
•
Fastener shank diameter
•
Concrete aggregate
Sintering Zone
Compression Zone
Fastener point magnified at sintering zone
3.2.1.1.2 Depth of Penetration into Concrete Generally, as the fastener penetration increases, so does the load capacity (1). However, a penetration depth which is too shallow or too deep may cause an increase in fastening failure (2). Depth of Penetration Guide1 Material Concrete block and joints Average concrete (2000-4000 psi) Precast or pre-stressed concrete (5000 psi +)
Sprinkler Installations with W10 Stud Only
Typical 3/4" to 1" (19 to 25 mm) 3/4" to 1-1/4" (19 to 32 mm) 3/4" to 1" (19 to 25 mm)
– 1" to 1-5/8" (25 to 41 mm) 1" to 1-1/4" (25 to 32 mm)
1 For allowable load capacities at specific embedment depths refer to specific product sections.
3.2.1.1.3 Compressive Strength of Concrete/Aggregate Hardness Generally, as the concrete compressive strength increases, so does the fastener’s load capacity (1). However, very high compressive strength and aggregate hardness decrease the possibility of making a successful fastening (2). Concrete Compressive Strength Optimum
2000 – 6000 psi (14-41 MPa)
Maximum
*8500 psi (55 MPa)
* May require predrilling with DX-Kwik system (Section 3.2.1.1.10)
3.2.1.1.4 Fastener Spacing, Edge Distance & Base Material Thickness Requirements for Concrete Nail Shank Diameter Smin in. (mm)
0.118 (3.0)
2-3/8 (60)
2-3/8 (60)
0.138 (3.5)
2-3/4 (70)
2-3/4 (70)
0.145 (3.7)
2-3/4 (70)
2-3/4 (70)
0.157 (4.0) (X-U)
2-3/4 (70)
2-3/4 (70)
0.177 (4.5) (X-AL-H)
2-3/4 (70)
2-3/4 (70)
0.177 (4.5) (DS)
3-1/8 (80)
3-1/8 (80)
0.205 (5.2) (W10)
4 (104)
Smin
C min= Min. Edge Distance1 S min = Min. Fastener Spacing t II = Min. Concrete Thickness = 3 x Fastener Penetration Depth2
Cmin
t II
Cmin in. (mm)
Depth of Penetration
dnom in. (mm)
1 Unless otherwise noted in corresponding load tables (e.g. sill plate application). 2 Unless otherwise noted in corresponding load tables (e.g. lightweight concrete over metal deck applications)
4 (104)
3.2.1.1.5 Maximum Tightening Torque Tmax
Maximum Tightening Torque, Tmax, for Threaded Studs Driven into Concrete, ft-lb (Nm) X-W6 3.0 (4.0)
Stud Type X-CR W6 3.0 (4.0)
W10 4.5 (6.0)
20 Hilti, Inc. (US) 1-800-879-8000 | www.us.hilti.com I en español 1-800-879-5000 I Hilti (Canada) Corp. 1-800-363-4458 I www.hilti.ca I Product Technical Guide 2008
02_3.0_DX_Mod15.QXD:H440.04_03 DX.QXD
12/30/07
12:49 AM
Page 21
General Construction Fastening Systems
General Construction Fastener Design & Selection 3.2.1
3.2.1.1.6 Fastener Locations when Installing into Lightweight Concrete over Metal Deck Hilti Powder-Driven Fastener 3,000 psi Lightweight Concrete
12"
min. 3-1/4" 3" Form Deck Lower Flute Location Upper Flute Location
4-1/2" min.
Direction of shear load on fastener
4-1/2" min.
7-1/4" min.
1-1/8" Min. Edge Distance Direction of tension load on fastener
Figure 1 – Hilti Fastener Location in 3” Deep Composite Floor Deck Normal Deck Profile Orientation
Hilti Power-Driven Fastener 6"
3,000 psi Lightweight Concrete
Direction of shear load on fastener
Form Deck Upper Flute Location Lower Flute Location
Direction of tension load on fastener
7/8" Edge Distance
1-3/4"
min. 2-1/2"
1-1/2"
2-1/2" 3-1/2"
Figure 2 – Hilti Fastener Location in 1-1/2” Deep Composite Floor Deck Normal Deck Profile Orientation
Hilti Power-Driven Fastener 6"
3,000 psi Lightweight Concrete
Form Deck
min. 2-1/2"
Direction of shear load on fastener
Upper Flute Location Lower Flute Location
Direction of tension load on fastener
1-3/4" Edge Distance
1-3/4"
1-1/2" 3-1/2"
Figure 3 – Hilti Fastener Location in 1-1/2” Deep Composite Floor Deck Inverted Deck Profile Orientation
Hilti, Inc. (US) 1-800-879-8000 | www.us.hilti.com I en español 1-800-879-5000 I Hilti (Canada) Corp. 1-800-363-4458 I www.hilti.ca I Product Technical Guide 2008 21
02_3.0_DX_Mod15.QXD:H440.04_03 DX.QXD
12/30/07
12:49 AM
Page 22
General Construction Fastening Systems
3.2.1 General Construction Fastener Design & Selection 3.2.1.1.7 Bending Moments on Power-Actuated Fasteners in Concrete As with concrete anchors, bending moments on poweractuated fasteners installed in concrete and masonry base materials can be minimized through proper design detailing and installation practice. Proper design should include redundancy with multiple fastening points instead of singlepoint fastenings, in order to distribute bending moment effects amongst multiple fasteners. Installation of threaded rod coupler hangers on powder-actuated threaded studs should be done with the coupler run down over the stud shank and in contact with the concrete or masonry base material as depicted in the figure below. Care should be taken not to Arrangements to reduce or prevent moment on shank:
exceed the maximum torque discussed in Section 3.2.1.1.5. Although no design equations are provided for determining equivalent bending moment loads on power-actuated fasteners, recommended allowable bending moments are provided in the table below based on testing with a safety factor of 2:1 for static loading. Relatively small bending moments can contribute to a significant reduction in the overall fastening capacity and must be checked by the engineer.
Arrangement causing moment to act on shank:
Non-symmetric arrangement: • Moment on fastened part • Prying effect must be considered in determining loads acting on fastener
Coupler not tight against concrete Coupler tight against concrete
For information on concrete anchor bolt bending, reference Sections 4.1.8.4 and 4.1.9.8. Allowable Bending Moments For Threaded Stud Fasteners Installed in Minimum 2,000 psi Concrete1 Fastener Designation X-W6 X-CR W6 W10
Mrec ft-lb (Nm) 3.6 (4.9) 3.2 (4.3) 10.0 (13.6)
1 Based on a safety factor greater than or equal to 2.0.
3.2.1.1.8 Combined Loading of Power-Actuated Fasteners in Concrete Combined loading of power-actuated fasteners installed in concrete can be treated with exponent α = 1 unless otherwise provided for the specific application (e.g. ceiling clips with power-actuated fasteners with 45° loading).
(Ns / Nrec)α + (Vs / Vrec)α ≤ 1.0 where: Ns = Applied Tension Load Vs = Applied Shear Load
Nrec = Allowable Tension Load Vrec = Allowable Shear Load
3.2.1.1.9 Fastener Clamping & Nailhead Stand-Off Powder-actuated fastenings must be thought of in terms of a fastening system consisting of the powder-actuated tool, cartridges and the fastener itself. Not all powder-actuated fastening systems can achieve adequate embedment and proper clamping of the fastened part to the base material. The installer should start with the lowest power regulation and cartridge and work up until tight clamping is achieved. Installers should never “double-shoot” fastenings with
excessive nail head stand-off in order to drive them deeper. This can create a safety hazard and break the bond or sintering between the fastener shank and the base material.
22 Hilti, Inc. (US) 1-800-879-8000 | www.us.hilti.com I en español 1-800-879-5000 I Hilti (Canada) Corp. 1-800-363-4458 I www.hilti.ca I Product Technical Guide 2008
02_3.0_DX_Mod15.QXD:H440.04_03 DX.QXD
12/30/07
12:49 AM
Page 23
General Construction Fastening Systems
General Construction Fastener Design & Selection 3.2.1 3.2.1.1.10 DX Kwik System 3.2.1.1.10.1 Product Description DX-KWIK is a method of fastening into concrete that combines the speed and portability of powder-actuated fastenings with the performance and consistency of anchors. The DX-KWIK System requires a shallow, small diameter hole to be drilled into the concrete, then a powderactuated fastener is driven through the hole into the concrete. Product Features Two very important fastening principles are achieved by using the DX-KWIK System:
•
The fastener obtains its holding power in the concrete deeper than standard powder-actuated fastenings without pre-drilling
•
Concrete stresses are distributed deeper below the concrete surface
DX-KWIK Fasteners
DX-KWIK System Advantages •
Higher allowable loads
•
Ability to fasten into high-strength concrete
•
Virtually eliminates concrete surface spalls
•
More consistent fastening
TE 7 A Rotary Hammer Drill
DX 460 Powder-Actuated Fastening Tool
DX-Kwik
Anchor
Standard DX
3.2.1.1.10.2 Installation Instructions
23 mm
5 mm Ø
1. Drill a hole into the concrete using a TX-C 5/18 or TX-C 5/23 special DX-KWIK Bit.
2. Insert the special high strength fastener into the DX tool leaving the fastener point protruding out.
3. Using the required cartridge power drive the fastener into the concrete.
Note: • Typically, DX-KWIK Fasteners are 47 mm minimum in length. • As of publication date, only X-U and X-AL-H series fasteners have been tested. Reference Section 3.2.2.3 for allowable load capacity table.
Hilti, Inc. (US) 1-800-879-8000 | www.us.hilti.com I en español 1-800-879-5000 I Hilti (Canada) Corp. 1-800-363-4458 I www.hilti.ca I Product Technical Guide 2008 23
02_3.0_DX_Mod15.QXD:H440.04_03 DX.QXD
12/30/07
12:49 AM
Page 24
General Construction Fastening Systems
3.2.1 General Construction Fastener Design & Selection 3.2.1.2 Fastening to Steel 3.2.1.2.1 General Suitability A fastener driven into steel is influenced by the following factors:
When a powder or gas-actuated fastener is driven into steel, the steel around the fastener shank is displaced. This displaced steel flows back around the shank and into the knurling creating a keying hold or in the case of smooth shank fasteners a friction hold. In addition, the heat generated during the driving process, at temperatures of approximately 1650°F, causes partial fusion of the fastener to the steel.
•
Base steel thickness
•
Tensile strength of base steel
•
Fastener spacing and edge distance
•
Fastener shank diameter
3.2.1.2.2 Fastener Spacing, Edge Distance & Base Material Thickness Requirements for Steel Cmin = Min. Edge Distance = 1/2" (12 mm)1
Smin
Smin = Min. Fastener Spacing without reduction in performance = 1" (25 mm)1 t II = Min. Base Steel Thickness = 1/8" (3 mm)
Cmin
t II
1 Unless otherwise noted (e.g. X-BT fastener)
Base Steel Thickness
Holding Power
3.2.1.2.3 Base Steel Thickness and Fastener Driving Distance Requirements
Optimum Thickness 3/8" to 1/2" (10 to 12 mm)
Steel Thickness
Application Range for Standard Knurled Fasteners
Base Steel Tensile Strength (x1000) psi
Optimal holding power is obtained when fastener point is driven to distance h ET.
As the tensile strength of the base steel increases, the thickness of the base steel suitable for DX fastenings decreases.
Nail Type tI LS
hET
LS
hET
L S = hET + t I * The objective of this table is to ensure adequate through-penetration of the base steel. For load capacity of fasteners without through-penetration, refer to corresponding allowable load table and applicable footnotes for more details.
X-U X-EDNI X-EW6H-xx-9 EDS X-EGN X-EW10H-xx-14 X-DNI DS X-S13 P8THP X-S16 P8TH X-ZF X-CR X-AL-H
Recommended Driving Distance to Achieve Optimal Tension Capacity, h ET*
in. 0.394 - 0.551 0.394 - 0.551 0.315 - 0.433 0.472 - 0.669 0.315 - 0.433 0.512 - 0.630 0.591 - 1.063 0.669 - 1.063 0.394 - 0.472 > 0.433 0.591 - 1.063 > 0.394 0.591 - 1.063
mm 10 - 14 10 - 14 8 - 11 12 - 17 8-11 13 - 16 15 - 27 17 - 27 10-12 > 11 15 - 27 > 10 15 - 27
24 Hilti, Inc. (US) 1-800-879-8000 | www.us.hilti.com I en español 1-800-879-5000 I Hilti (Canada) Corp. 1-800-363-4458 I www.hilti.ca I Product Technical Guide 2008
02_3.0_DX_Mod15.QXD:H440.04_03 DX.QXD
12/30/07
12:49 AM
Page 25
General Construction Fastening Systems
General Construction Fastener Design & Selection 3.2.1
X-U
DNI
DS
X-AL-H
Wood Thickness (mm)
3.2.1.2.4 Recommended Fastener Lengths for Attaching Wood to Steel Base Material Application Limit X-U DNI Fasteners Application Limit Fasteners
Up to 1/4" (6 mm)
5/16" (8 mm) 3/8" (10 mm) 7/16" (11 mm) 1/2" (12 mm)
Base Material Thickness Notes: 1 X-U, DNI, DS or X-AL-H up to 62 mm long may be used in base steel up to 1/4" (6 mm) thick. 2 If the application limit is exceeded, shank buckling can occur. 3 Numbers in ● and ■ represent fastener length in mm.
3.2.1.2.5 Recommendations for Attaching Steel to Steel Base Material t I ≤ 1/8 in. (3 mm)
Note
1 Directly fastened material ≤ 1/8" thick usually deforms with the displaced base material. This allows a tight fit between the fastened steel and base material without the need for pre-drilling.
3.2.1.2.6 Maximum Tightening Torque Tightening-Torque
Tmax
Maximum Tightening Torque, Tmax, for Threaded Studs Driven into Steel, ft-lb (Nm) Stud Type Tmax
X-EW6H
X-EM8H
X-EW10H
X-CRM8
X-BT W10 & X-BT M8
3.0 (4.1)
8.0 (10.8)
11.0 (14.9)
6.0 (8.1)
6.0 (8.1)
Hilti, Inc. (US) 1-800-879-8000 | www.us.hilti.com I en español 1-800-879-5000 I Hilti (Canada) Corp. 1-800-363-4458 I www.hilti.ca I Product Technical Guide 2008 25
02_3.0_DX_Mod15.QXD:H440.04_03 DX.QXD
12/30/07
12:49 AM
Page 26
General Construction Fastening Systems
3.2.1 General Construction Fastener Design & Selection 3.2.1.2.7 Bending Moments on Power-Actuated Fasteners in Steel As with weld studs, bending moments on power-actuated fasteners installed in steel can be minimized through proper design detailing and installation practice. Proper design should include redundancy with multiple fastening points instead of single-point fastenings, in order to distribute bending moment effects amongst multiple fasteners. Installation of threaded rod coupler hangers on powder-actuated threaded studs should be done with the coupler run down over the stud shank and in contact with the steel base material as depicted in the figure below. Care should be taken not to exceed the maximum torque discussed in Section 3.2.1.2.6.
Arrangements to reduce or prevent moment on shank:
Although no design equations are provided for determining equivalent bending moment loads on power-actuated fasteners, recommended allowable bending moments are provided in the table below based on testing with a safety factor of 2:1 for static loading Relatively small bending moments can contribute to a significant reduction in the overall fastening capacity and must be checked by the engineer.
Arrangement causing moment to act on shank:
Non-symmetric arrangement: • Moment on fastened part • Prying effect must be considered in determining loads acting on fastener
Coupler not tight against steel
Coupler tight against steel
Allowable Bending Moments For Threaded Stud Fasteners Installed in Minimum ASTM A 36 Steel1 Fastener Nomenclature X-EW6H X-EM8H X-EW10H X-CRM8 X-BT M8/W10
Mrec ft-lb (Nm) 2.2 (3.0) 4.5 (6.2) 6.5 (8.8) 4.0 (5.5) 6.0 (8.2)
1 Based on a safety factor greater than or equal to 2.0.
3.2.1.2.8 Combined Loading of Power-Actuated Fasteners in Steel Combined loading of power-actuated fasteners installed in steel can be treated with exponent α = 1 unless otherwise provided for the specific application (e.g. powder-actuated fasteners for steel deck applications with diaphragm shear and tension uplift).
Hilti powder-actuated fasteners for attachment of steel decks (X-ENP-19 L15, X-EDN19 THQ12 and X-EDNK22 THQ12) have separate design equations for combined loading in the SDI Deck Diaphragm Design Manual, 3rd Edition (2006).
(Ns / Nrec)α + (Vs / Vrec)α ≤ 1.0 where: Ns = Applied Tension Load Vs = Applied Tension Load
Nrec = Allowable Tension Load Vrec = Allowable Tension Load
26 Hilti, Inc. (US) 1-800-879-8000 | www.us.hilti.com I en español 1-800-879-5000 I Hilti (Canada) Corp. 1-800-363-4458 I www.hilti.ca I Product Technical Guide 2008
02_3.0_DX_Mod15.QXD:H440.04_03 DX.QXD
12/30/07
12:49 AM
Page 27
General Construction Fastening Systems
General Construction Fastener Design & Selection 3.2.1 3.2.1.3 Power-Actuated Fastener Selection Guide
X-U Fastener
X-U MX Magazine
DS/EDS Fastener
X-ZF Fastener
X-ZF MX Fastener Collated
For universal, high quality fastenings to concrete and steel: perimeter wall applications, forming, underfloor, trunking, thin metal brackets, angles, etc. High-volume, repetitive fastenings to concrete and steel: perimeter wall applications, forming installation, etc.
A standard quality fastener for fastenings to concrete and CMU block
X-DNI/X-EDNI Fastener
For fastening to concrete (X-DNI) and steel (X-EDNI), forming, underfloor, trunking, installation straps, thin metal, brackets, angles, etc.
X-AL-H High-Strength Fastener
DX 600N
DX 76
DX 460
DX 36
Page Numbers
• • • • •
3.2.2 3.2.3 3.2.4
31-36 37-39 40-44
M
3.2.2 3.2.3 3.2.4
31-36 37-39 40-44
3.2.2 3.2.4
31-36 40-44
• • • • •
3.2.2
31-36
M
M
3.2.2
31-36
• • • • •
3.2.2
31-36
• • • • •
3.2.2
31-36
M
M
3.2.2
31-36
M
3.2.2
31-36
• • • • •
3.2.2
31-36
M
P10
• •
High volume repetitive fastenings to concrete and CMU block
Corrosion resistance equivalent to SAE 316 stainless steel for exterior or corrosive environments
X-EDNI MX Fastener Collated
2008 Product Technical Guide Section Numbers
For fastening to concrete (DS) and steel (EDS): perimeter wall applications, forming, underfloor, trunking, installation straps, thin metal, brackets, angles, etc.
X-CR Corrosion Resistant Fastener
X-DNI MX Fastener Collated
DX 351
•
DX 35
Fastener Notes: = Single M = Collated Fasteners (magazine required) P8 = 8 mm fastener guide required P10 = 10 mm fastener guide required Fastener Application
DX E72
Hilti Fastening Tool
High-volume, repetitive fastenings to concrete, forming installation, etc.
Fastenings to steel: angles, brackets, channels, tracks, etc.
For high performance fastening to high strength concrete and steel Note: Special drive piston is required
Источник: [https://torrent-igruha.org/3551-portal.html]A guide to specification and installation
Hilti. Outperform. Outlast. P.O. Box 21148, Tulsa, OK 74121 • Hilti, Inc. (US) 1-800-879-8000 www.us.hilti.com • Servicio al Cliente en español 1-800-879-5000 • Hilti (Canada) Corporation 1-800-363-4458 www.ca.hilti.com • Hilti is an equal opportunity employer Hilti is a registered trademark of Hilti, Corp. ©Copyright 2006 by Hilti, Inc. • H440 • 3004711 • 1/08 HA The data contained in this literature was current as of the date of publication. Updates and changes may be made based on later testing. If verification is needed that the data is still current, please contact the Hilti Technical Support Specialists at 1-800-879-8000. All published load values contained in this literature represent the results of testing by Hilti or test organizations. Local base materials were used. Because of variations in materials, on-site testing is necessary to determine performance at any specific site. Laser beams represented by red lines in this publication. Printed in the United States
*ISO 14001 US Only
2008 Edition
Prod_Tech_Guide_Cover_2008.qxd:MI_Kapitel_5_en.qxd
12/29/07
2:16 PM
Page 4
Hilti Product Technical Guide
P R O F I S
PROFIS: The World’s Most Powerful Anchor Design Software • Easy to Learn – Start working in just minutes • Fast and Powerful – Produce detailed designs quickly • Specify with Confidence – The largest number of approvals and latest design codes No charge. Download now at www.us.hilti.com or www.hilti.ca
Hilti Online • • • • • • •
Technical Library Design Centers Interactive Product Advisors Full-line Product Catalog Online Ordering Maps to Hilti locations “Contact Us” program to answer your questions
Firestop Systems When it comes to Life Safety and building code compliance, Hilti provides complete solutions with a wide range of products and unmatched technical support. • Firestop Systems Guides - Through Penetrations - Joint Penetrations • FACT Program • FS 411 • BASIC Training • Engineering Judgements • Firestop Design Center online at www.us.hilti.com or www.hilti.ca
Hilti Diaphragm Deck Design The Hilti Diaphragm Deck Design Program allows designers to quickly and accurately design roof deck and composite floor deck diaphragms. • Ability to design with innovative Hilti fasteners for frame and sidelap connection • Creates easy to use load tables with span ranges based on user input • Allows for different safety factors depending on load type, building code and field quality control • Direct link to Hilti website
MI – Industrial Pipe Support Technical Guide A guide to specifying the Hilti modular pipe support system for medium to heavy loads without welding. • MI System is the ideal solution for pipes up to 24 in. diameter • Reliable fastenings without welds • Easily installed
Hilti, Inc. (US) 1-800-879-8000 | www.us.hilti.com I en español 1-800-879-5000 I Hilti (Canada) Corp. 1-800-363-4458 I www.ca.hilti.com I Product Technical Guide 2008
01_Intro_.QXD:H440.06_0102 IntroGenInf.QXD
12/30/07
12:45 AM
Page 1
Hilti Product Technical Guide
Table of Contents Table of Contents
Introduction
1.0
2
Fastening Technology
2.0
3
Direct Fastening Systems
3.0
16
Anchoring Systems
4.0
128
Construction Chemicals
5.0
390
Installation Systems
6.0
404
Reference
7.0
438
Hilti, Inc. (US) 1-800-879-8000 | www.us.hilti.com I en español 1-800-879-5000 I Hilti (Canada) Corp. 1-800-363-4458 I www.hilti.ca I Product Technical Guide 2008 1
01_Intro_.QXD:H440.06_0102 IntroGenInf.QXD
12/30/07
12:45 AM
Page 2
Hilti Product Technical Guide
1.0 Introduction 1.1 About Published Load Values
1.3 Our Purpose
The Product Technical Guide is intended to supplement the
We passionately create enthusiastic customers and build a better future!
Hilti Product Catalog with technical information for the designer or specifier. Technical data presented herein was current as of the date of publication (see back cover). Load values are based on testing and analytical calculations by Hilti or by contracted testing laboratories using testing procedures and construction materials representative of current practice in North America. Load values obtained from testing represent the average results of multiple identical samples. Variations in base materials such as concrete and local site conditions require on-site testing to determine actual performance at any specific site. Data may also be based on national standards or professional research and analysis. Note that design values published in reports issued by approval agencies (e.g., ICC-ES, COLA, etc.) may differ from those contained in this Product Technical Guide. For information regarding updates and changes, please contact Hilti,Inc. (US) Technical Support at 1-800-879-8000 or Hilti (Canada) Corporation at 1-800-363-4458.
1.2 Units Technical data is provided in both fractional (Imperial) and metric units. Metric values are provided using the International System of units (SI) in observance the Metric Conversion Act of 1975 as amended by the Omnibus Trade and Competitiveness Act of 1988. Data for metric products, such as the HSL and HDA anchors, is provided in SI units with conversions to Imperial engineering units (inches, pounds, and so forth) given in parentheses. Data for fractional products (e.g. the Kwik Bolt 3) is provided in Imperial engineering units with the SI metric conversions shown in parentheses. Additional information may be found in Section 8.3.1 Metric Conversions and Equivalents, provided in this Product Technical Guide.
Enthusiastic Customers We create success for our customers by identifying their needs and providing innovative and value-adding solutions. Build a better future We embrace our responsibility towards society and environment.
1.4 Our Quality System Hilti is one of a select group of North American companies to receive the ISO 9001 and ISO 14001 Certifications. This recognition of our commitment to quality ensures our customers that Hilti has the systems and procedures in place to maintain our position as the world market leader, and to continually evaluate and improve our performance. That’s Total Customer Satisfaction! For Technical Support, contact Hilti,Inc. (US) at 1-800-8798000 or Hilti (Canada) Corporation at 1-800-363-4458.
2 Hilti, Inc. (US) 1-800-879-8000 | www.us.hilti.com I en español 1-800-879-5000 I Hilti (Canada) Corp. 1-800-363-4458 I www.hilti.ca I Product Technical Guide 2008
01_Intro_.QXD:H440.06_0102 IntroGenInf.QXD
12/30/07
12:45 AM
Page 3
Fastening Technology
Base Materials 2.1 2.1.1 Base Materials for Fastening The design of modern buildings requires fastenings to be made in a variety of base materials. To meet this challenge, fastener manufacturers have developed many products specifically targeting certain types of base materials. The properties of the base material play a decisive role in the suitability and performance of a fastener. The designer must carefully match the type of fastener with the base material to obtain the desired results. There is hardly a base material in which a fastening cannot be made with a Hilti product.
2.1.2 Concrete Concrete is a mineral building material which is made from three basic ingredients; cement, aggregate and water. Special additives are also used to influence or change certain properties. Concrete has a relatively high compressive strength compared to its tensile strength. Thus, steel reinforcing bars are cast in concrete to carry the tensile forces, and this combination is referred to as reinforced concrete. Cement is the binding agent which combines with water and aggregate and hardens through the process of hydration to form concrete. Portland cement is the most common cement and is available in several different types, as outlined in ASTM C 150, to meet specific design requirements. The aggregates used in concrete consist of both fine aggregate (usually sand) and coarse aggregate graded by particle size. Different types of aggregates can be used to create concrete with specific characteristics. Normal weight concrete is generally made from crushed stone or gravel. Lightweight concrete is used when it is desirable to reduce the dead load on a structure or to achieve a superior fire rating for a floor structure. Lightweight aggregates are made from expanded clay, shale, slate or blast-furnace slag. Lightweight insulating concrete is used when thermal insulating properties are a prime consideration. Lightweight insulating aggregates are manufactured from perlite, vermiculite, blast-furnace slag, clay or shale. Sand lightweight concrete is made from lightweight aggregate and natural sand. All concrete with a unit weight between 85 and 115 pcf is considered to be structural lightweight concrete. The ASTM specification and unit weight for each of these concretes is summarized as follows:
ASTM Concrete Type Normal Weight Sand Lightweight All Lightweight Lightweight Insulating Concrete
Aggregate Grading Specification
Concrete Unit Weight pcf
ASTM C 33 ASTM C 330 ASTM C 330 ASTM C 332
145-155 105-115 85-110 15-90
The type and mechanical properties of concrete aggregate have a major influence on the behavior of drill bits used to drill anchor holes. The harder the aggregates cause higher bit wear and reduced drilling performance. The hardness of concrete aggregate can also affect the load capacity of power-actuated fasteners and anchors. Driven fasteners or studs can generally penetrate “soft” aggregates (shale or limestone), but hard aggregates (like granite) near the surface of the concrete can adversely affect the penetration of a fastener or stud and reduce its load capacity. The effect of aggregate mechanical properties on anchor performance is less well understood, although in general harder/denser aggregates such as granite tend to result in higher concrete cone breakout loads, whereas lightweight aggregates produce lower tension and shear capacities. Values for the ultimate strength of fasteners in concrete are traditionally given in relation to the 28-day uniaxial compressive strength of the concrete (actual, not specified). Concrete which has cured for less than 28 days is referred to as green concrete. Aggregate type, cement replacements such as fly ash, and admixtures could have an effect on the capacity of some fasteners, and this may not be reflected in the concrete strength as measured in a uniaxial compression test. Generally, Hilti data reflects testing with common aggregates and cement types in plain, unreinforced concrete. In questionable cases, consult with Hilti Technical Support. In view of the significantly lower strength of green concrete (less than 28-day cure), it is recommended that anchors and power-actuated fastenings not be made in cast-in-place concrete which has cured for less than 7 days, unless site testing is performed to verify the fastening capacity. If an anchor is installed in green concrete, but not loaded until the concrete has achieved full cure, the capacity of the anchor can be based on the strength of the concrete at the time of loading. Power-actuated fastening capacity should be based on the concrete strength at the time of installation. Cutting through concrete reinforcement when drilling holes for anchors should be avoided. If this is not possible, the responsible design engineer should be consulted first.
Hilti, Inc. (US) 1-800-879-8000 | www.us.hilti.com I en español 1-800-879-5000 I Hilti (Canada) Corp. 1-800-363-4458 I www.hilti.ca I Product Technical Guide 2008 3
01_Intro_.QXD:H440.06_0102 IntroGenInf.QXD
12/30/07
12:45 AM
Page 4
Fastening Technology
2.1 Base Materials 2.1.3 Masonry Materials
8"
Masonry is a heterogeneous building material consisting of brick, block or clay tile bonded together using joint mortar. The primary application for masonry is the construction of walls which are made by placing masonry components in horizontal rows (course) and vertical rows (wythe). Masonry components are manufactured in a wide variety of shapes, sizes, materials and both hollow and solid configurations. These variations require that the selection of an anchoring or fastening system be carefully matched to the application and type of masonry material being used. As a base material, masonry generally has a much lower strength than concrete. The behavior of the masonry components, as well as the geometry of their cavities and webs, has a considerable influence on the ultimate load capacity of the fastening. When drilling holes for anchors in masonry with hollow cavities, care must be taken to avoid spalling on the inside of the face shell. This could greatly affect the performance of “toggle” type mechanical anchors whose length must be matched to the face shell thickness. To reduce the potential for spalling, holes should be drilled using rotation only (i.e. hammering action of the drill turned off).
2.1.3.1 Concrete Block Concrete block is the term which is commonly used to refer to concrete masonry units (CMU) made from Portland cement, water and mineral aggregates. CMUs are manufactured in a variety of shapes and sizes using normal weight and lightweight aggregates. Both hollow and solid load bearing CMUs are produced in accordance with ASTM C90. Nominal Width of Unit in. (mm)
Minimum face-shell ThicknessA in. (mm)
3 (76) and 4 (102) 6 (152)
Minimum web ThicknessA in. (mm)
3/4 (19)
3/4 (19)
1 (25)
1 (25)
8 (203)
1-1/4 (32)
1 (25)
10 (254)
1-3/8 (35) 1-1/4 (32)B
1-1/8 (29)
1-1/2 (38) 1-1/4 (32)B
1-1/8 (29)
≥12 (305)
7 5\8"
7 5\8"
8"
16"
Nominal Size (usually fictitious)
15 5\8"
Modular Size (actual)
CMU sizes generally refer to the nominal width of the unit (6”, 8”, 10” etc.). Actual dimensions are nominal dimensions reduced by the thickness of the mortar joint. Concrete block construction can be reinforced, whereby reinforcing bars are placed vertically in the cells and those cells are filled with grout to create a composite section analogous to reinforced concrete. If all cells, both unreinforced and reinforced, are filled with grout, the construction is referred to as fully grouted. If only the reinforced cells are grouted, the construction is referred to as partially grouted. Horizontal reinforcing may be placed in the wall via a bond beam, which is always grouted. Ladder reinforcement may also be placed in the mortar bed between courses. Grout typically conforms to ASTM C476 and has a compressive strength of at least 2,000 psi. Concrete masonry units have a compressive strength which may range from 1,250 to over 4,800 psi, although the maximum specified compressive strength of the assembled masonry will generally not exceed 3,000 psi. In general, both chemical and mechanical anchors may be used in grouted CMU. If voids are present or suspected, mechanical anchors should not be used, and chemical anchors should only be installed in conjunction with a screen tube to prevent uncontrolled flow of the bonding material. In ungrouted CMU, anchor strength is generally assumed to be derived from the face shell thickness, which can be variable.
Adapted from ASTM C 90. A Average of measurements on three units taken at the thinnest point. B This face-shell thickness is applicable where the allowable design load is reduced in proportion to the reduction in thickness from the basic face-shell thickness shown.
4 Hilti, Inc. (US) 1-800-879-8000 | www.us.hilti.com I en español 1-800-879-5000 I Hilti (Canada) Corp. 1-800-363-4458 I www.hilti.ca I Product Technical Guide 2008
01_Intro_.QXD:H440.06_0102 IntroGenInf.QXD
12/30/07
12:45 AM
Page 5
Fastening Technology
Base Materials 2.1 2.1.3.2 Brick
2.1.3.4 Mortar
Bricks are prismatic masonry units made from suitable mixture of soil, clay and a stabilizing agent (emulsified asphalt). They are shaped by molding, pressing or extruding and are fired at elevated temperature to meet the strength and durability requirements of ASTM C62 for solid brick and C652 for hollow brick.
Mortar is the product which is used in the construction of reinforced and non-reinforced unit masonry structures. The role of mortar when hardened in the finished structure is to transfer the compressive, tensile and shear stresses between the units. Mortar consists of a mixture of cementitious material, aggregate and water combined in accordance with ASTM C270. Either a cement/lime mortar or a masonry mortar, each in four types, can be used under this specification. Mortar
Depending upon the grade, brick (solid clay masonry) can have a compressive strength ranging from 1,250 to over 25,000 psi. 12" Brick Grouted multi-wyte masonry construction Bearing Walls typically consists of two wythes, each one unit masonry in thickness, separated by a space 2” to 4-1/2” in width, which is filled with grout. The wythes are connected with wall ties. This space may also be reinforced with vertical reinforcing bars. Solid brick masonry consists of abutting wythes interlaced with header courses. In general, chemical anchors are recommended for use in brick. In older unreinforced construction (URM), or where the condition of the masonry is unknown, it is advisable to use a screen tube to prevent unrestricted flow of the bonding material into voids.
2.1.3.3 Clay Tile Structural clay load-bearing wall tile is made from clay or shale and heat treated (fired) at an elevated temperature to develop the strength and durability required by ASTM C34. These units are manufactured in a variety of shapes and sizes with one or more cavities and develop a compressive strength of 500 to 1000 psi depending upon the grade and type. These units typically have a 3/4" face shell thickness and 1/2" interior web thickness.
Cement-Lime
Masonry Cement
Type
M S N O M S N O
Average Compressive Strength at 28 Days, Min psi (MPa)
2500 1800 750 350 2500 1800 750 350
(17.2) (12.4) (5.2) (2.4) (17.2) (12.4) (5.2) (2.4)
Since mortar plays a significant role in the structural integrity of the masonry wall, it is important to understand how post installed anchors interact with the structure. Within a masonry structure there are designated joint locations. The proximity of a post-installed anchor or power-actuated fastener to one of these locations must be considered in the design of the anchorage. Product specific guidelines are provided within the guide.
2.1.3.5 Grout ACI defines grout as “a mixture of cementitious material and water, with or without aggregate, proportioned to produce a pourable consistency without segregation of the constituents”. The terms grout and mortar are frequently used interchangeably but are, in actuality, not the same. Grout need not contain aggregate (mortar contains fine aggregate). Grout is supplied in a pourable consistency where mortar is not. Grout fills voids while mortar bonds elements together. Grout is used to fill space or cavities and provide continuity between building elements. In some applications, grout will act in a structural capacity, such as in unreinforced masonry construction.
Clay tile as a base material is somewhat more difficult to anchor to due to the thin face shell and low compressive strength. Adhesive anchors such as the Hilti HIT HY 20 with a wire screen are usually recommended because they spread the load over a larger area and do not produce expansion forces.
Grout, in regards to post-installed anchorages, is specified by the design official. When post-installed anchors are tested for the development of design values, the grout is specified according to applicable ASTM standards. Design engineers are encouraged to become familiar with the characteristics of the grout used in performance testing to better understand the applicability of the design loads published in this guide to the actual jobsite.
Hilti, Inc. (US) 1-800-879-8000 | www.us.hilti.com I en español 1-800-879-5000 I Hilti (Canada) Corp. 1-800-363-4458 I www.hilti.ca I Product Technical Guide 2008 5
01_Intro_.QXD:H440.06_0102 IntroGenInf.QXD
12/30/07
12:45 AM
Page 6
Fastening Technology
2.1 Base Materials 2.1.4 Gypsum Wallboard Gypsum wall board consists of an incombustible core, essentially gypsum, surfaced with paper firmly bonded to the core. It is made in flat sheets 4 feet by 8 feet or larger, and from 1/4" to 5/8" thick in accordance with ASTM C 1396/C 1396M. Gypsum wallboard is attached to the wall studs and ceiling joints in residential and commercial building to form the base for the finished wall or ceiling treatment. Gypsum wall board does not have the capacity to accept high loads. Hilti offers several light duty anchors designed for use in gypsum wallboard.
2.1.5 Light Gauge Steel Framing Light gauge steel framing uses cold-formed steel sections for the construction of walls, floors and roofs. The framing memers have industry standard dimensions similar to wood framing studs. There are a large variety of shapes and sizes available for both residential and commercial markets. Framing members are generally produced in C-sections with thicknesses of 12 to 25 GA and varying widths. Other specialized shapes and connection components are also available from a variety of manufacturers. Design of light gauge steel framing is done in accordance with the American Iron and Steel Institute (AISI) Cold-Formed Steel Design Manual. Powder-actuated fasteners, self-drilling screws and anchors are commonly used in light gauge steel construction. Powderactuated fasteners and anchors are used to attach the light gauge steel to concrete and steel base materials. Self-drilling screws are used to attach light gauge steel components as part of larger assemblies or systems. Fasteners are typically evaluated without the steel elements. The elements should be evaluated separately based on applicable AISI design requirements. In some instances, such as steel deck diaphragms, deflection slip clips and perimeter wall track at edge of slab, powder-actuated fasteners have been tested with the light gauge steel components as a system assembly and the corresponding data is provided in this Product Technical Guide.
2.1.6 Autoclave Aerated Concrete Precast autoclaved aerated concrete (AAC) is a lightweight, precast building material of a uniform porous structure. Adding aluminum powder to a cement, lime, fine sand and water mixture causes it to expand dramatically. After mixing, the slurry is poured into a mold and allowed to “rise”. The product is removed from its mold after a few hours and fed through a cutting machine, which sections the AAC into
predetermined sizes. These AAC products are then placed into an autoclave and steam cured for 10 to 12 hours. Autoclaving initiates a second chemical reaction that transforms the material into a hard calcium silicate. AAC was developed in Europe and is currently being manufactured in the United States by licensed facilities. Strength Class
Average Compressive Strength, psi (N/mm2)
Average Comp. Str. Density lb/ft3 (g/cm3)
AAC - 2 AAC - 4 AAC - 6
360 (2.5) 725 (5.0) 1090 (7.5)
32 (0.5) 38 (0.6) 44 (0.7)
Due to the low compressive strength of AAC, anchors that spread the load over the entire embedded section are preferred (e.g., HUD, HRD, adhesives).
2.1.7 Steel Structural steel is a critical building component which serves as the main structural support in many structures. Iron ore is processed and combined with other elements to produce different types of steel. Reference to a particular type of steel is usually made by ASTM standard. For example, ASTM A36 is the specification for what is usually referred to as A36 steel. Steel is hot-rolled into structural shapes that are available in different grades, with the grade corresponding to the yield strength. Common grades of structural steel include ASTM A36, which has a minimum yield strength of 36 ksi and ASTM A572, which is available in grades 42, 50, 55, 60 and 65. ASTM A992 is a high strength steel used extensively for wide flanged shapes. The grade of steel is very important when selecting a power actuated fastener. The grade and thickness determine the resistance that must be overcome when setting the fastener. The power required to drive a fastener must be greater than the resistance. If the power and resistance are too high, the fastener could be damaged during the setting process. This is referred to as exceeding the application range for the fastener. For a given fastener, the application range is determined by its length, diameter, material strength and hardness.
2.1.8 Pre-tensioned/ Pre-stressed Concrete Pre-tensioned / prestressed concrete is concrete that is cast around already tensioned tendons or strands. This method produces a good bond between the tendon and concrete, which both protects the tendon from corrosion and allows for direct transfer of tension. The cured concrete adheres and bonds to the bars and when the tension is released it is transferred to the concrete as compression by static friction. Most pre-tensioned / prestressed concrete elements are prefabricated in a factory and must be transported to the construction site, which limits their size.
6 Hilti, Inc. (US) 1-800-879-8000 | www.us.hilti.com I en español 1-800-879-5000 I Hilti (Canada) Corp. 1-800-363-4458 I www.hilti.ca I Product Technical Guide 2008
01_Intro_.QXD:H440.06_0102 IntroGenInf.QXD
12/30/07
12:45 AM
Page 7
Fastening Technology
Evaluation of Test Data 2.2 Pre-tensioned / prestressed concrete poses a unique problem when post-installed anchors and power-actuated fasteners are used. Drilling into the concrete is typically not recommended unless a precise knowledge of the location of the tendons is known. Since locating the tendons can be tedious and expensive other alternatives for post-installed anchors are needed. Typically, the clear cover over the tendons is known and can be used to provide connection points. Post-installed anchors and power-actuated fasteners with embedments on the magnitude of 3/4" to 1” are typically ideal and do not interfere with the tendons or strands.
2.1.9 Bonded Post-tensioned Concrete Bonded post-tensioned concrete is a term used for a method of applying compression after pouring concrete and the curing process. This method is commonly used to create monolithic slabs. Slabs are created in-situ versus being manufactured at a plant. The same considerations for avoiding post-tensioning strands should be considered when using post-installed anchors and power-actuated fasteners.
2.1.10 Admixtures Chemical admixtures are the ingredients in concrete other than Portland cement, water and aggregate that are added to the mix immediately before or during mixing. Chemical admixtures are used to enhance the properties of concrete and mortar in the plastic and hardened state. These properties may be modified to increase compressive and flexural strength at all ages, decrease permeability and improve durability, inhibit corrosion, reduce shrinkage, accelerate or retard initial set, increase slump and workability, improve pumpability and finishability, increase cement efficiency, and improve the economy of the mixture. An admixture or combination of admixtures may be the only feasible means of achieving the desired results. Testing of post-installed anchors and power-actuated fasteners is performed in concrete without admixtures. Designers should take into consideration the affects of admixtures to the concrete when determining the applicability of particular post-installed anchors or power-actuated fasteners.
2.2.1 Developing Fastener Performance Data Hilti published data is based on laboratory testing unless otherwise indicated. However, the emergence of accurate predictive methods, as embodied in the Concrete Capacity Design (CCD) method, allows for calculation of anchor capacity for a variety of design conditions. The CCD method is applicable to anchors for which pre-qualification testing has been performed in accordance with the testing standard developed by ACI Committee 355.
Fastener testing at Hilti is conducted in accordance with ASTM E 488, Standard Test Methods for Strength of Anchors in Concrete and Masonry Elements, ASTM E 1512 Standard Test Methods for Testing Bond Performance of Bonded Anchors and ASTM E 1190 Standard Test Methods for Strength of Power-Actuated Fasteners Installed in Structural Members. Because of the wide variation in possible concrete reinforcing configurations found in construction, testing is typically performed in unreinforced concrete, which gives conservative results. There are two methods of developing allowable loads; (1) apply an appropriate safety factor to the mean ultimate load as determined from a given number of individual tests, or (2) apply a statistical method to the test data which relates the allowable working load to the performance variability of the fastening.
2.2.2 Allowable Loads Historically, allowable loads for anchors have been derived by applying a global safety factor to the average ultimate value of test results. This approach is characterized by Eq. 2.2.1. Eq. 2.2.1
Fall =
F v
Where: F = mean of test data (population sample) v = safety factor Global safety factors of 4 to 8 for post-installed anchors have been industry practice for nearly three decades. The global safety factor is assumed to cover expected variations in field installation conditions and variation in anchor performance from laboratory tests. Note that global safety factors applied to the mean do not explicitly account for anchor coefficient of variation, i.e., all anchors are considered equal with respect to variability in the test data.
2.2.3 Statistical Evaluation of Data Experience from a large number of tests on anchors has shown that ultimate loads generally approximate a normal Gaussian probability density function as shown in Fig. 2.2.1. This allows for the use of statistical evaluation techniques that relate the resistance to the system performance variability associated with a particular anchor. One such technique is to adjust the mean such that the resulting resistance represents a so-called 5% fractile, or characteristic value. As commonly applied, the characteristic load, Rk, for a given test series is derived from the mean, F, the standard deviation, s, and the sample size, n, such that, for a 90% probability (90% confidence) 95% of the loads are above
Hilti, Inc. (US) 1-800-879-8000 | www.us.hilti.com I en español 1-800-879-5000 I Hilti (Canada) Corp. 1-800-363-4458 I www.hilti.ca I Product Technical Guide 2008 7
01_Intro_.QXD:H440.06_0102 IntroGenInf.QXD
12/30/07
12:45 AM
Page 8
Fastening Technology
2.2 Evaluation of Test Data
Wahrscheinlichkeitsdichte Probability density
Frequency Häufigkeit [%] (%)
the characteristic load. The characteristic load is calculated according to Eq. 2.2.2 whereby k is usually provided by a onesided population limit for a standard distribution for sample size n. Histogram of the Histogramm der Versuchsergebnisse test results
Probability density Wahrscheinlichkeitsdichte
R Rkk
FFrec ALL Frec Rk F ALL==Rk/ν
on the characteristic resistance. Unless stated otherwise, the following safety factors are applied to the characteristic resistance: v
=
3 for concrete and bond failure modes
v
=
5 for shallow anchors (due to the greater variability associated with cover concrete) and plastic anchors
These safety factors are intended to cover the following conditions, within reasonably expected variations: Ru,m F
Versagenslast Ultimate Load
v
Fig. 2.2.1 Frequency distribution of fastener loads, demonstrating the significance of the 5% fractile and the allowable load As applied to the characteristic resistance, the global safety factor, v, is not required to account for the variability of the system. This allows for a tighter definition of the components to be covered by the safety factor, such as concrete variability and the variability of lab test data with respect to field performance. (Taken together with an ultimate strength design method, whereby loading variability is accommodated via load factors, the partial safety factors associated with these effects can be converted into a strength reduction factor, f, thus allowing for greater consistency in the safety factor). Fastening systems exhibiting tightly grouped test data are rewarded with a low standard deviation, s.
1. variability of anchor performance in the field with respect to laboratory performance 2. variability of actual loading with respect to calculated loads 3. typical variability of base material (e.g., concrete) condition with respect to specified or laboratory conditions 4. reasonable installation deviations Note that installation error, e.g., installation not in accordance with Hilti’s installation instructions, is not covered by the safety factor. It is the responsibility of the user or design engineer to examine all factors that could influence an anchorage and to adjust the design resistance accordingly.
Fall = Rk = F - k · s = F (1 - k · cv) v v v
Eq. 2.2.2 Where: Rk
=
characteristic resistance of the tested anchor system
F
=
mean ultimate resistance of the tested anchor system
k
=
distribution value for test sample size n
s
=
standard deviation of the test data
cv
=
coefficient of variation = s F
v
=
safety factor
Many of the allowable loads in this Technical Guide are based
8 Hilti, Inc. (US) 1-800-879-8000 | www.us.hilti.com I en español 1-800-879-5000 I Hilti (Canada) Corp. 1-800-363-4458 I www.hilti.ca I Product Technical Guide 2008
01_Intro_.QXD:H440.06_0102 IntroGenInf.QXD
12/30/07
12:45 AM
Page 9
Fastening Technology
Corrosion 2.3 2.3.1 The Corrosion Process
Galvanic Series of Metals and Alloys
Corrosion is defined as the chemical or electrochemical reaction between a material, usually a metal, and its environment that produces a deterioration of the material and its properties (ASTM G 15). The corrosion process can be very complex and have many contributing factors that lead to immediate or delayed destructive results. In anchorage and fastener design, the most common types of corrosion are direct chemical attack and electro-chemical contact.
Corroded End (anodic, or least noble) Magnesium Magnesium alloys Zinc Aluminum 1100 Cadmium Aluminum 2024-T4 Steel or Iron Cast Iron Chromium-iron (active) Ni-Resist cast iron Type 304 Stainless (active) Type 316 Stainless (active) Lead tin solders Lead Tin Nickel (active) Inconel nickel-chromium alloy (active) Hastelloy Alloy C (active) Brasses Copper Bronzes Copper-nickel alloys Monel nickel-copper alloy Silver solder Nickel (passive) Inconel nickel-chromium alloy (passive) Chromium-iron (passive) Type 304 Stainless (passive) Type 316 Stainless (passive) Hastelloy Alloy C (passive) Silver Titanium Graphite Gold Platinum Protected End (cathodic, or most noble)
2.3.2 Types of Corrosion 2.3.2.1 Direct Chemical Attack Corrosion by direct chemical attack occurs when the base material is soluble in the corroding medium. One method of mitigating these effects is to select a fastener that is not susceptible to attack by the corroding chemical. Compatibility tables of various chemical compounds with Hilti adhesive and epoxy fastening systems are provided in this Product Technical Guide. When selection of a base metal compatible with the corroding medium is not possible or economical, another solution is to provide a coating that is resistant to the corroding medium. These might include metallic coatings such as zinc or organic coatings such as epoxies or fluorocarbons.
2.3.2.2 Electrochemical Contact Corrosion All metals have an electrical potential relative to each other and have been ranked accordingly to form the “electromotive force series” or galvanic series of metals. When metals of different potential come into contact in the presence of an electrolyte (moisture), the more active metal with more negative potential becomes the anode and corrodes, while the other metal becomes the cathode and is galvanically protected. The severity and rate of attack will be influenced by: a. Relative position of the contacting metals in the galvanic series, b. Relative surface areas of the contacting materials and, c. Conductivity of the electrolyte. The effects of electro-chemical contact corrosion may be mitigated by: a. Using similar metals close together in the electromotive force series,
Source: IFI Fastener Standards, 6th Edition
b. Separating dissimilar metals with gaskets, plastic washers or paint with low electrical conductivity. Materials typically used in these applications include: 1. High Density Polyethylene (HDPE) 2. Polytetrafluoroethylene (PTFE) 3. Polycarbonates 4. Neoprene / chloroprene 5. Cold galvanizing compound 6. Bituminous coatings or paint Note: Specifiers must ensure that these materials are compatible with other anchorage components in the service environment. c. Selecting materials so that the fastener is the cathode, most noble or protected component, d. Providing drainage or weep holes to prevent entrapment of the electrolyte
Hilti, Inc. (US) 1-800-879-8000 | www.us.hilti.com I en español 1-800-879-5000 I Hilti (Canada) Corp. 1-800-363-4458 I www.hilti.ca I Product Technical Guide 2008 9
01_Intro_.QXD:H440.06_0102 IntroGenInf.QXD
12/30/07
12:45 AM
Page 10
Fastening Technology
2.3 Corrosion 2.3.2.3 Hydrogen Assisted Stress Corrosion Cracking Often incorrectly referred to as hydrogen embrittlement, hydrogen assisted stress corrosion cracking (HASCC) is an environmentally induced failure mechanism that is sometimes delayed and most times occurs without warning. HASCC occurs when a hardened steel fastener is stressed (loaded) in a service environment which chemically generates hydrogen (such as when zinc and iron combine in the presence of moisture). The potential for HASCC is directly related to steel hardness. The higher the fastener hardness, the greater the susceptibility to stress corrosion cracking failures. Eliminating or reducing any one of these contributing factors (high steel hardness, corrosion or stress) reduces the overall potential for this type of fastener failure. Hydrogen embrittlement, on the other hand, refers to a potential damaging side effect of the steel fastener manufacturing process, and is unrelated to project site corrosion. Hydrogen embrittlement is neutralized by proper processing during fastener pickling, cleaning and plating operations, specifically by “baking” the fasteners after the application of the galvanic coating.
2.3.3 Corrosion Protection The most common material used for corrosion protection of carbon steel fasteners is zinc. Zinc coatings can be uniformly applied by a variety of methods to achieve a wide range of coating thickness depending on the application. All things being equal, thicker coatings typically provide higher levels of protection. An estimating table for the mean corrosion rate and service life of zinc coatings in various atmospheres is provided to the right. These values are for reference only, due to the large variances in the research findings and specific project site conditions, but they can provide the specifier with a better understanding of the expected service life of zinc coatings. In controlled environments where the relative humidity is low and no corrosive elements are present, the rate of corrosion of zinc coatings is approximately 0.15 microns per year.
Atmosphere
Mean Corrosion Rate
Industrial Urban Non-Industrial or Marine Suburban Rural Indoors
5.6 µm/year 1.5 µm/year 1.3 µm/year 0.8 µm/year Considerably less than 0.5 µm/year
Source: ASTM B 633 Appendix X1. Service Life of Zinc
2.3.3.1 Suggested Corrosion Resistance Use of AISI 316 stainless steel in environments where pitting or stress corrosion is likely should be avoided due to the possibility of sudden failure without visual warning. Fastenings in these applications should be regularly inspected for serviceability condition. See chart 2.3.3.1 below.
Corrosion Resistance
Typical Conditions of Use
Phosphate and Oil Coatings (Black Oxide)
• Interior applications without any particular influence of moisture
Zinc electro-plated 5 – 10 µm • Interior applications without any (ASTM B 633, SC 1, Type III) particular influence of moisture Organic Coatings – • If covered sufficiently by Kwik Cote ≥ 17.8 µm noncorrosive concrete Mechanically deposited zinc coating 40 – 107 µm Hot-Dip Galvanizing (HDG) > 50 µm (ASTM A 153)
• Interior applications in damp environments and near saltwater (ASTM B 695) • Exterior applications in only slightly corrosive atmospheres
Sherardizing Process > 50 µm Stainless Steel (AISI 303 / 304)
• Interior applications where heavy condensation is present • Exterior applications in corrosive environments
Stainless Steel (AISI 316)
• Near saltwater • Exterior corrosive environments
Zinc coatings can be applied to anchors and fasteners by different methods. These include (in order of increasing coating thickness and corrosion protection): a. ASTM B 633 – Standard Specification for Electrodeposited Coatings of Zinc on Iron and Steel b. ASTM B 695 – Standard Specification for Coatings of Zinc Mechanically Deposited on Iron and Steel c. ASTM A 153 – Standard Specification for Zinc Coating (Hot-Dip) on Iron and Steel Hardware d. Sherardizing Process – Proprietary Diffusion Controlled Zinc Coating Process
10 Hilti, Inc. (US) 1-800-879-8000 | www.us.hilti.com I en español 1-800-879-5000 I Hilti (Canada) Corp. 1-800-363-4458 I www.hilti.ca I Product Technical Guide 2008
01_Intro_.QXD:H440.06_0102 IntroGenInf.QXD
12/30/07
12:45 AM
Page 11
Fastening Technology
Corrosion 2.3 2.3.4 Test Methods Various test methods have been used in the development of Hilti fastening systems to predict performance in corrosive environments. Some of the internationally accepted standards and test methods used in these evaluations are: a. ASTM B 117 Standard Practice for Operating Salt Spray (Fog) Apparatus b. ASTM G 85 Standard Practice for Modified Salt Spray (Fog) Testing c. ASTM G 87 Standard Practice for Conducting Moist SO2 Tests d. DIN 50021 – SS Salt Spray Testing (ISO 3768) e. DIN 50018 2,0 Kesternich Test (ISO 6988) Testing in a Saturated Atmosphere in the Presence of Sulfur Dioxide
2.3.5 Hilti Fastening Systems 2.3.5.1 Anchors Most Hilti metal anchors are available in carbon steel with an electrodeposited zinc coating of at least 5 µm with chromate passivation. Chromate passivation reduces the rate of corrosion for zinc coatings, maintains color, abrasion resistance and when damaged, exhibits a unique “self healing” property. This means that the chromium contained within the film on the anchor surface will repassivate any exposed areas and lower the corrosion rate. Hilti standard and super HAS threaded rods in 7/8" diameter size are zinc coated to at least 50 µm by the hot-dip galvanizing process. Other sizes may be available through special orders. Where the long-term integrity of a fastening is important, and there is a risk of corrosion of a carbon steel anchor, then a stainless steel anchor may be specified. It must be noted that under certain extreme conditions, even stainless steel anchors will corrode and additional protective measures will be needed. Stainless steels should not be used when the anchorage will be subjected to long term exposure, immersion in chloride solutions, or in corrosive environments where the average temperature is above 86° F. Hilti HCR High Corrosion Resistant threaded rod is available on a special order basis. It provides superior corrosion resistance to AISI 316 and is an alternative to titanium or other special stainless steels.
2.3.5.2 Power-Actuated Fasteners Hilti carbon steel power-actuated fasteners are typically zinc plated to a minimum thickness of 5 µm for limited corrosion resistance. Another method used to resist corrosion for the Hilti carbon steel ENP series decking fasteners is the use of the stainless steel SDK2 sealing cap with an integrated neoprene seal. Please see Section 3.4.1.3.1. Hilti also manufactures stainless steel X-CR powder-actuated nails and threaded studs. The X-CR fasteners are made from a proprietary material with corrosion resistance equivalent to AISI 316 material, but with higher strength and hardness. Because carbon steel power-actuated fasteners are hardened, they can be susceptible to HASCC. It is, therefore, important to evaluate the suitability of the application prior to use if the environment may be corrosive. If in doubt, stainless steel X-CR fasteners are recommended.
2.3.5.3 Screw Fasteners Hilti screw fasteners are available with three different types of coatings: a. phosphate and oil (black oxide) b. zinc electroplated c. Kwik-Cote Black oxide offers the lowest resistance to corrosion and generally restricts use to interior finishing applications. Hilti Kwik-Cote is a proprietary copolymer organic coating that helps protect against galvanic corrosion in a manner similar to zinc. Zinc electro-plating is in accordance with ASTM B 633 SC 1 Type III to a minimum thickness of 5 µm. Hilti provides the proprietary Kwik-Cote organic coating on certain types of Kwik-Pro screws and all Kwik-Flex screws. Stainless steel screws (AISI 410 or 300 series) and sealing washers are available on a special order basis. Warning: Because of the potential for HASCC failures, standard hardened carbon steel fasteners are not recommended for use with dissimilar metals or chemically treated wood when moisture may be present or in corrosive environments. For screws that are resistant to HASCC, consider using Hilti Kwik-Flex screws.
Note: Specifiers should also consult ACI 318-05 Chapter 4 Durability Requirements, Section 4.4 and Tables 4.4.1 and 4.2.2 for applications where concrete structures will be exposed to chloride ion concentrations, deicing chemicals, salt, salt water, brackish water, seawater or spray from these sources.
Hilti, Inc. (US) 1-800-879-8000 | www.us.hilti.com I en español 1-800-879-5000 I Hilti (Canada) Corp. 1-800-363-4458 I www.hilti.ca I Product Technical Guide 2008 11
01_Intro_.QXD:H440.06_0102 IntroGenInf.QXD
12/30/07
12:45 AM
Page 12
Fastening Technology
2.3 Corrosion 2.3.6 Applications It is difficult to offer generalized solutions to corrosion problems. An applications guide can be useful as a starting point for fastener material selection. The specifier should also consult: a. Local and national building code requirements (e.g., IBC, UBC) b. Standard practice manuals for specific types of construction (e.g., ACI, PCI, AISC, PCA, CRSI, AASHTO, NDS/APA) c. Manufacturers of structural components d. Hilti technical support
2.3.6.1 General Applications8 Application
Conditions
Fastener Recommendations
Structural steel components to concrete & masonry (interior connections within the building envelope not subjected to free weathering) 1, 2
Interior applications without condensation
Galvanic zinc plating
Interior applications with occasional condensation
HDG or Sherardized
Structural steel components to concrete & masonry (exterior connections subjected to free weathering) 1,2
Slightly corrosive environments
HDG or Sherardized
Highly corrosive environments
Stainless steel
Zinc coated or painted metal decking to steel beam / joist connections with roof membrane or cover 3, 4, 5
Interior applications without condensation
Galvanic zinc plating or Kwik-Cote
Exposed deck applications subject to free weathering 3, 4, 5
With sealing washers (SDK2)
Galvanic zinc plating
Without sealing washers (SDK2)
X-CR
Composite deck applications (steel connections with concrete overlayment) 1
Covered sufficiently by non-corrosive concrete
Galvanic zinc plating
Insulation fastenings / EIFS fastenings 6
Applications without condensation
Galvanic zinc plating or Kwik-Cote
Applications with condensation
X-CR
Interior applications
Galvanic zinc plating
Exterior applications
HDG or Sherardized
Parking garages / parking decks subject to periodic application of de-icers including chloride solutions 7
Non-safety critical
HDG, Sherardized or X-CR1
Safety critical
Stainless steel1
Road / bridge decks subject to periodic application of de-icers including chloride solutions
Non-safety critical
HDG or Sherardized
Safety critical
Stainless steel
Temporary formwork, erection bracing and short-term scaffolding
1 2 3 4 5 6 7 8
Refer to ACI 318 Chapter 4 – Durability Refer to ACI 530.1 Section 2.4F – Coatings for Corrosion Protection Refer to SDI “A Rational Approach to Steel Deck Corrosion Protection” Refer to Factory Mutual Approval Standard Class No. 4450 Section 5.4 Refer to Factory Mutual Approval Standard Class No. 4470 Section 5.6 Refer to ICC Evaluation Services Acceptance Criteria 24 – Exterior Insulation and Finish Systems Refer to PCI Parking Structures: Recommended Practice for Design & Construction – Chapters 3, 5 and Appendix General guidelines address environmental corrosion (direct chemical attack). Additional considerations should be taken into account when using hardened steel fasteners susceptible to HASCC.
12 Hilti, Inc. (US) 1-800-879-8000 | www.us.hilti.com I en español 1-800-879-5000 I Hilti (Canada) Corp. 1-800-363-4458 I www.hilti.ca I Product Technical Guide 2008
01_Intro_.QXD:H440.06_0102 IntroGenInf.QXD
12/30/07
12:45 AM
Page 13
Fastening Technology
Corrosion 2.3 2.3.6.2 Special Applications These application charts are offered as general guidelines.4 Site specific conditions may influence the decision. Application
Conditions
Fastener Recommendations
Aluminum fastenings (flashing / roofing accessories, hand rails, grating panels, sign posts and miscellaneous fixtures)
Interior applications without condensation
Galvanic zinc plating or Kwik-Cote
Exterior applications with condensation
Stainless steel, X-CR
Not submerged
HDG, Sherardized or Stainless steel
Submerged
Stainless steel 2
Not submerged
HDG, Sherardized or Stainless steel
Submerged
Stainless steel 2
Non-safety critical or temporary connections
HDG, Sherardized or X-CR
High humidity with the presence of chlorides – splash zone
Stainless steel1
On the off-shore platform or rig
Stainless steel or X-CR
Non-safety critical
HDG or Sherardized, X-CR
Safety critical or subjected to high concentrations of soluble chlorides
Stainless steel1
Above grade
HDG
Below grade
Stainless steel, X-CR
Non-safety critical
HDG or Stainless steel
Safety critical or subjected to high concentrations of SO2
Stainless steel, X-CR1
Non-safety critical
HDG, Stainless steel or X-CR
Safety critical
Stainless steel1
Water treatment
Waste water treatment
Marine (salt water environments, shipyards, docks, off-shore platforms)
Indoor swimming pools
Pressure / chemically treated wood 3
Power plant stacks / chimneys
Tunnels (lighting fixtures, rails, guardposts)
1 2 3 4
Steel selection depends on safety relevance Must electrically isolate fastener from contact with concrete reinforcement through use of adhesive or epoxy anchoring system, gasket or plastic washer with low electrical conductivity Refer to APA Technical Note No. D485D and AF & PA Technical Report No. 7 General guidelines address environmental corrosion (direct chemical attack). Additional considerations should be taken into account when using hardened steel fasteners susceptible to HASCC.
Hilti, Inc. (US) 1-800-879-8000 | www.us.hilti.com I en español 1-800-879-5000 I Hilti (Canada) Corp. 1-800-363-4458 I www.hilti.ca I Product Technical Guide 2008 13
01_Intro_.QXD:H440.06_0102 IntroGenInf.QXD
12/30/07
12:45 AM
Page 14
Fastening Technology
Notes
14 Hilti, Inc. (US) 1-800-879-8000 | www.us.hilti.com I en español 1-800-879-5000 I Hilti (Canada) Corp. 1-800-363-4458 I www.hilti.ca I Product Technical Guide 2008
01_Intro_.QXD:H440.06_0102 IntroGenInf.QXD
12/30/07
12:45 AM
Page 15
Fastening Technology
Notes
Hilti, Inc. (US) 1-800-879-8000 | www.us.hilti.com I en español 1-800-879-5000 I Hilti (Canada) Corp. 1-800-363-4458 I www.hilti.ca I Product Technical Guide 2008 15
01_Intro_.QXD:H440.06_0102 IntroGenInf.QXD
12/30/07
12:45 AM
Page 16
Direct Fastening Systems
Direct Fastening Systems Table of Contents Section
Description
3.1 3.1.1 3.1.2 3.1.3
Direct Fastening Terminology & Applications . . . . . . . . . . . . . . . . . . . . . . . . . . . . . . . . . . . 18 Direct Fastening Terminology . . . . . . . . . . . . . . . . . . . . . . . . . . . . . . . . . . . . . . . . . . . . . . . . . . 18 Benefits of Direct Fastening systems . . . . . . . . . . . . . . . . . . . . . . . . . . . . . . . . . . . . . . . . . . . . 19 Common Direct Fastening Applications . . . . . . . . . . . . . . . . . . . . . . . . . . . . . . . . . . . . . . . . . . 19
3.2 3.2.1 3.2.1.1 3.2.1.2 3.2.1.3
General Construction Fastening Systems . . . . . . . . . . . . . . . . . . . . . . . . . . . . . . . . . . . . . . 20 General Construction Fastener Design & Selection . . . . . . . . . . . . . . . . . . . . . . . . . . . . . . . . . 20 Fastening to Concrete . . . . . . . . . . . . . . . . . . . . . . . . . . . . . . . . . . . . . . . . . . . . . . . . . . . . . . . 20 Fastening to Steel . . . . . . . . . . . . . . . . . . . . . . . . . . . . . . . . . . . . . . . . . . . . . . . . . . . . . . . . . . . 24 Fastener Selection Guide . . . . . . . . . . . . . . . . . . . . . . . . . . . . . . . . . . . . . . . . . . . . . . . . . . . . . 27
3.2.2
Page
General Application Fasteners . . . . . . . . . . . . . . . . . . . . . . . . . . . . . . . . . . . . . . . . . . . . . . . . . 31 X-U, DS, EDS, X-ZF, X-S13, X-DAK, X-DNI, X-EDNI, X-GN, X-EGN and X-GHP fastener series for general applications to concrete, steel or masonry
3.2.3
X-U Universal Knurled Shank Fastener . . . . . . . . . . . . . . . . . . . . . . . . . . . . . . . . . . . . . . . . . . 37 Universal X-U fastener for use in concrete, steel or masonry
3.2.4
Perimeter Wall Application Fasteners . . . . . . . . . . . . . . . . . . . . . . . . . . . . . . . . . . . . . . . . . . . . 40 X-U, DS and EDS fasteners for attachment of perimeter track and deflection slip clips to concrete or steel
3.2.5
Drywall Track Fastening Systems . . . . . . . . . . . . . . . . . . . . . . . . . . . . . . . . . . . . . . . . . . . . . . . 45 X-S13, X-DAK, X-DW, X-S16, X-GN, X-EGN, and X-GHP fastener series for attachment of drywall track to concrete, steel or masonry
3.2.6
Sill Plate Fastening Systems . . . . . . . . . . . . . . . . . . . . . . . . . . . . . . . . . . . . . . . . . . . . . . . . . . 49 X-CF 72, X-ZF 72, X-DNI 72, X-CP 72, and X-CR-L 72 fasteners for attachment of wood sill plates to concrete
3.2.7
Ceiling Clip & Hanger Assemblies . . . . . . . . . . . . . . . . . . . . . . . . . . . . . . . . . . . . . . . . . . . . . . 51 Sheet steel clips with pre-mounted powder-actuated fasteners with or without pre-tied wire for suspending acoustical ceiling grids and panels from concrete
3.2.8
Stud Fasteners for Attachment to Concrete . . . . . . . . . . . . . . . . . . . . . . . . . . . . . . . . . . . . . . 53 Carbon steel (1/4” and 3/8”) and stainless steel (1/4”) powder-actuated threaded studs for attachment to concrete
3.2.9
Stud Fasteners for Attachment to Steel . . . . . . . . . . . . . . . . . . . . . . . . . . . . . . . . . . . . . . . . . . 56 Carbon steel (1/4”, 3/8” and 8mm) and stainless steel (3/8” and 8mm) powder-actuated threaded studs for attachment to steel
3.2.10
.
X-BT Fastening Systems . . . . . . . . . . . . . . . . . . . . . . . . . . . . . . . . . . . . . . . . . . . . . . . . . . . . . 59 Innovative X-BT (3/8” and 8mm) blunt-tip threaded stud fastener for attachment to coated or painted steel
3.2.11
Clips & Hangers for Mechanical and Electrical Applications . . . . . . . . . . . . . . . . . . . . . . . . . . 64 Threaded and smooth rod hangers (X-HS and X-RH), cable holders, clamps and tie fasteners (X-ECH, X-EKB MX, and X-ECT) and conduit clips (X-BX, X-EMTC and X-EMTSC MX) for use in miscellaneous mechanical and electrical applications
3.2.12
Insulation or Soft Material Attachment Fasteners . . . . . . . . . . . . . . . . . . . . . . . . . . . . . . . . . . 69 X-IE and X-SW fasteners for attachment of insulation and other soft materials to concrete, masonry or steel
16 Hilti, Inc. (US) 1-800-879-8000 | www.us.hilti.com I en español 1-800-879-5000 I Hilti (Canada) Corp. 1-800-363-4458 I www.hilti.ca I Product Technical Guide 2008
02_3.0_DX_Mod15.QXD:H440.04_03 DX.QXD
12/30/07
12:49 AM
Page 17
Direct Fastening Systems
Direct Fastening Systems Table of Contents Section
Description
3.3 3.3.1
Grating & Checkerplate Fastening Systems . . . . . . . . . . . . . . . . . . . . . . . . . . . . . . . . . . . . 71 Grating & Checkerplate Fastener Selection . . . . . . . . . . . . . . . . . . . . . . . . . . . . . . . . . . . . . . . 71
3.3.2
Page
X-FCM & X-FCP Grating & Checkerplate Fastening Systems . . . . . . . . . . . . . . . . . . . . . . . . . 72 Removable and reusable grating (X-FCM) & checkerplate (X-FCP) fastening systems available in zinc plated, HDG, and stainless steel corrosion resistance and consisting of a disk that threads onto a powder-actuated threaded stud. Stainless steel version specifically designed for off-shore
3.3.3
X-GR, X-GR RU, & X-MGR Grating Fastening Systems . . . . . . . . . . . . . . . . . . . . . . . . . . . . . 77 Permanent (X-GR), or removable (X-GR RU and X-MGR) grating fastening systems with HDG equivalent corrosion resistance for attachment of grating in on-shore industrial applications
3.4 3.4.1 3.4.1.1 3.4.1.2 3.4.1.3 3.4.1.4 3.4.1.5 3.4.1.6 3.4.1.7 3.4.2
Steel Deck Fastening Systems . . . . . . . . . . . . . . . . . . . . . . . . . . . . . . . . . . . . . . . . . . . . . . . 82 Steel Deck Fastener Design & Selection . . . . . . . . . . . . . . . . . . . . . . . . . . . . . . . . . . . . . . . . . 82 Steel Deck Terminology & Definitions . . . . . . . . . . . . . . . . . . . . . . . . . . . . . . . . . . . . . . . . . . . . 82 Steel Deck Diaphragm Design & Theory . . . . . . . . . . . . . . . . . . . . . . . . . . . . . . . . . . . . . . . . . 84 Fastener, Tool & Cartridge Selection Guide . . . . . . . . . . . . . . . . . . . . . . . . . . . . . . . . . . . . . . . 90 Submittal Information for Roof Deck . . . . . . . . . . . . . . . . . . . . . . . . . . . . . . . . . . . . . . . . . . . . 94 Submittal Information for Floor Deck . . . . . . . . . . . . . . . . . . . . . . . . . . . . . . . . . . . . . . . . . . . . 95 Fastener Quantity Estimation Table . . . . . . . . . . . . . . . . . . . . . . . . . . . . . . . . . . . . . . . . . . . . . 96 Common Steel Deck Dimensions . . . . . . . . . . . . . . . . . . . . . . . . . . . . . . . . . . . . . . . . . . . . . . . 96 Deck Fasteners for Attachment to Bar Joist . . . . . . . . . . . . . . . . . . . . . . . . . . . . . . . . . . . . . . 97 X-EDN19 and X-EDNK22 fasteners for attachment of many types of steel deck to bar joist up to 3/8-inch thick
3.4.3
Deck Fasteners for Attachment to Structural Steel . . . . . . . . . . . . . . . . . . . . . . . . . . . . . . . . 103 X-ENP-19 fastener for attachment of many types of steel deck to structural steel greater than or equal to 1/4-inch thick
3.4.4
X-HVB Shear Connector . . . . . . . . . . . . . . . . . . . . . . . . . . . . . . . . . . . . . . . . . . . . . . . . . . . . . 109 Mechanically attached X-HVB shear connector for use in composite beam construction with steel beams and concrete slabs
3.5 3.5.1 3.5.1.1 3.5.1.2 3.5.1.3 3.5.1.4 3.5.1.5 3.5.2
Screw Fastening Systems . . . . . . . . . . . . . . . . . . . . . . . . . . . . . . . . . . . . . . . . . . . . . . . . . . 112 Self-Drilling Screw Fastener Selection and Design . . . . . . . . . . . . . . . . . . . . . . . . . . . . . . . . 112 Drill Point Selection . . . . . . . . . . . . . . . . . . . . . . . . . . . . . . . . . . . . . . . . . . . . . . . . . . . . . . . . 112 Thread Selection . . . . . . . . . . . . . . . . . . . . . . . . . . . . . . . . . . . . . . . . . . . . . . . . . . . . . . . . . . . 113 Head Style Selection . . . . . . . . . . . . . . . . . . . . . . . . . . . . . . . . . . . . . . . . . . . . . . . . . . . . . . . 114 Sealing Criteria . . . . . . . . . . . . . . . . . . . . . . . . . . . . . . . . . . . . . . . . . . . . . . . . . . . . . . . . . . . . 114 Length Selection . . . . . . . . . . . . . . . . . . . . . . . . . . . . . . . . . . . . . . . . . . . . . . . . . . . . . . . . . . . 114 Kwik-Pro Self-Drilling Screws . . . . . . . . . . . . . . . . . . . . . . . . . . . . . . . . . . . . . . . . . . . . . . . . . 115 Self-drilling screws available in a variety of head styles, thread lengths and drill-flute lengths for screw diameters #6 through 1/4” meeting ASTM C 1513 and SAE J78 or ASTM C954
3.5.3
Kwik-Flex Self-Drilling Screws . . . . . . . . . . . . . . . . . . . . . . . . . . . . . . . . . . . . . . . . . . . . . . . . 123 Self-drilling screws specifically designed to resist embrittlement that can be caused by stress, dissimilar metals and moisture available in HWH head style and diameters #10 through 5/16”
Hilti, Inc. (US) 1-800-879-8000 | www.us.hilti.com I en español 1-800-879-5000 I Hilti (Canada) Corp. 1-800-363-4458 I www.hilti.ca I Product Technical Guide 2008 17
02_3.0_DX_Mod15.QXD:H440.04_03 DX.QXD
12/30/07
12:49 AM
Page 18
Direct Fastening Systems
3.1 Direct Fastening Terminology & Applications 3.1.1 Direct Fastening Terminology DX = Hilti Powder-Actuated Direct Fastening System
Steel Deck Fastening Systems1
GX = Gas-Actuated Fastening Systems
tf
= flange thickness of beam or bar joist for steel decking applications, in. (mm)
Characteristics of Steel and Other Metals = specified minimum ultimate tensile strength of metals, ksi (MPa)
F
= diaphragm flexibility factor, in./lb (mm x 10-6/N)
G'
= diaphragm shear stiffness lb/in. (N/mm x 10-6)
= specified minimum yield strength of metals, ksi (MPa)
q
= allowable diaphragm shear, plf (N/mm)
Characteristics of Concrete and Masonry
Qf
= fastener strength, panel to frame, lb (kN)
fc
= concrete compressive strength as measured by testing of cylinder, psi (MPa)
Sf
= fastener flexibility factor, panel to frame, in./kip (mm/kN)
f'c
= specified concrete compressive strength, psi (MPa)
X-HVB Shear Connector
Fu
Fy
Fastening Details
hr
= nominal rib height, in. (mm)
cmin = minimum edge distance, in. (mm)
Hs
= connector height, in. (mm)
dnom = nominal fastener shank diameter, in. (mm)
Nr
= number of connectors in one rib
D
q
= allowable shear strength, lb (kN)
Qn
= nominal shear strength, lb (kN)
Rg
= coefficient to account for group effect
Rp
= position effect factor shear connectors
wr
= average width of rib, in. (mm)
= thread diameter for threaded studs, in. (mm)
hET = penetration of the fastener point below the surface of the base material, in. (mm) hNVS = nailhead stand-off above the surface fastened into. For nails, this is the surface of the fastened material. For threaded studs, the surface of the base material, in. (mm) Ls
= length of fastener, in. (mm)
Ycon = distance from top of steel beam to top of concrete slab, in. (mm)
smin = minimum fastener spacing, in. (mm)
Screw Fastening Systems 2
tI
= thickness of the fastened material, in. (mm)
L
= total thickness of the fastened material, where more than one layer fastened, in. (mm)
MT = maximum thickness of all attachments to be fastened, including the base material, in. (mm)
= thickness of the base material, in. (mm)
Pss = nominal shear strength (resistance) of screw, lb (kN)
ΣtI tII
Tmax = maximum tightening torque, ft-lb (Nm)
= length of screw, in. (mm)
Pts = nominal tension strength (resistance) of screw, lb (kN)
1 More detailed definitions for Steel Deck Fastening Systems can be found on page 82. 2 Terminology for screw fastener head styles (e.g. hex washer head (HWH)) can be found on page 114.
Fastener Nomenclature1 Fastener Series1
Washer Type2 and Diameter (mm)
X-U 37 P8 MX
Stud Nomenclature1
1. The fastener name preceded by an “E” (e.g. X-EDNI 16 P8), indicates a knurled shank for improved holding Indicates in steel. (Note: X-U fasteners have Collated Fastener knurling.) (strips of 10)
Shank Length (mm)
2. P = Plastic washer Thread Size S = Steel washer (mm) D = Double washer (1 plastic, 1 steel) L = Double washer (both steel) DP = Double washer (both plastic) FP = Ferrule and plastic guide washer
Shank Diameter
Washer Type2 and Diameter (mm)
X-W6 20 22 FP8
3. “MX” at the end of fastener name indicates fasteners collated in strips of 10
Washer
Thread Length (mm)
Shank Diameter
Washer
Shank Length (mm)
Thread Length
Thread Size
18 Hilti, Inc. (US) 1-800-879-8000 | www.us.hilti.com I en español 1-800-879-5000 I Hilti (Canada) Corp. 1-800-363-4458 I www.hilti.ca I Product Technical Guide 2008
02_3.0_DX_Mod15.QXD:H440.04_03 DX.QXD
12/30/07
12:49 AM
Page 19
Direct Fastening Systems
Direct Fastening Terminology & Applications 3.1 3.1.2 Benefits of Direct Fastening Systems Power-actuated fastening systems are recognized as a safe, acceptable and cost effective method of making instantaneous fastenings into various construction base materials such as concrete, steel and masonry. Poweractuated fastening technology uses either powder cartridges (blank cartridges) or compressed gas cartridges. Without the need for external power sources, it is portable, fast and lightweight allowing for reliable fastenings in difficult access areas on today’s construction sites.
Screw fastening systems are commonly used for the attachment of cold-formed steel members. Self-drilling screws allow for direct attachment without the need for additional equipment such as a drill bit or welding machine making screw fastening portable, fast and lightweight. A key benefit to using direct fastening systems is increased productivity for the end user due to the speed of making fastenings vs. drilling and anchoring or welding. Fastenings are easily inspected and suitable for all trades in a variety of applications.
3.1.3 Common Direct Fastening Applications General Fastenings to Concrete
General Fastenings to Steel
Reference Sections 3.2.2, 3.2.3 and 3.2.8
Reference Sections 3.2.2, 3.2.3 and 3.2.9
Interior Partition Walls (Drywall)
Wood Sill Plate Attachment
Ceiling Hangers
Reference Section 3.2.5
Reference Section 3.2.6
Reference Section 3.2.7
Electrical Grounding
Pipe Hangers
Cable & Conduit Attachment
Reference Section 3.2.10
Reference Section 3.2.11
Reference Section 3.2.11
Thermal Insulation Attachment
Grating & Checkerplate Attachment
Reference Section 3.2.12
Reference Section 3.3
Steel Deck Sidelap Attachment
Light Steel Framing Connections
Reference Sections 3.4 and 3.5
Perimeter Wall Applications - Deflection Slip Clips - Steel Framing Track Reference Section 3.2.4
Steel Deck Attachment Reference Section 3.4
Reference Section 3.5
Hilti, Inc. (US) 1-800-879-8000 | www.us.hilti.com I en español 1-800-879-5000 I Hilti (Canada) Corp. 1-800-363-4458 I www.hilti.ca I Product Technical Guide 2008 19
02_3.0_DX_Mod15.QXD:H440.04_03 DX.QXD
12/30/07
12:49 AM
Page 20
General Construction Fastening Systems
3.2.1 General Construction Fastener Design & Selection 3.2.1.1 Fastening to Concrete 3.2.1.1.1 General Suitability A fastener driven into concrete is influenced by the following factors:
When a powder or gas-actuated fastener is driven into concrete, the concrete around the fastener shank is displaced. This displaced concrete compresses against the shank creating a friction hold. In addition, heat generated during the driving process causes a sintering of the concrete to the fastener.
•
Depth of penetration
•
Compressive strength of the concrete
•
Fastener spacing and edge distance
•
Fastener shank diameter
•
Concrete aggregate
Sintering Zone
Compression Zone
Fastener point magnified at sintering zone
3.2.1.1.2 Depth of Penetration into Concrete Generally, as the fastener penetration increases, so does the load capacity (1). However, a penetration depth which is too shallow or too deep may cause an increase in fastening failure (2). Depth of Penetration Guide1 Material Concrete block and joints Average concrete (2000-4000 psi) Precast or pre-stressed concrete (5000 psi +)
Sprinkler Installations with W10 Stud Only
Typical 3/4" to 1" (19 to 25 mm) 3/4" to 1-1/4" (19 to 32 mm) 3/4" to 1" (19 to 25 mm)
– 1" to 1-5/8" (25 to 41 mm) 1" to 1-1/4" (25 to 32 mm)
1 For allowable load capacities at specific embedment depths refer to specific product sections.
3.2.1.1.3 Compressive Strength of Concrete/Aggregate Hardness Generally, as the concrete compressive strength increases, so does the fastener’s load capacity (1). However, very high compressive strength and aggregate hardness decrease the possibility of making a successful fastening (2). Concrete Compressive Strength Optimum
2000 – 6000 psi (14-41 MPa)
Maximum
*8500 psi (55 MPa)
* May require predrilling with DX-Kwik system (Section 3.2.1.1.10)
3.2.1.1.4 Fastener Spacing, Edge Distance & Base Material Thickness Requirements for Concrete Nail Shank Diameter Smin in. (mm)
0.118 (3.0)
2-3/8 (60)
2-3/8 (60)
0.138 (3.5)
2-3/4 (70)
2-3/4 (70)
0.145 (3.7)
2-3/4 (70)
2-3/4 (70)
0.157 (4.0) (X-U)
2-3/4 (70)
2-3/4 (70)
0.177 (4.5) (X-AL-H)
2-3/4 (70)
2-3/4 (70)
0.177 (4.5) (DS)
3-1/8 (80)
3-1/8 (80)
0.205 (5.2) (W10)
4 (104)
Smin
C min= Min. Edge Distance1 S min = Min. Fastener Spacing t II = Min. Concrete Thickness = 3 x Fastener Penetration Depth2
Cmin
t II
Cmin in. (mm)
Depth of Penetration
dnom in. (mm)
1 Unless otherwise noted in corresponding load tables (e.g. sill plate application). 2 Unless otherwise noted in corresponding load tables (e.g. lightweight concrete over metal deck applications)
4 (104)
3.2.1.1.5 Maximum Tightening Torque Tmax
Maximum Tightening Torque, Tmax, for Threaded Studs Driven into Concrete, ft-lb (Nm) X-W6 3.0 (4.0)
Stud Type X-CR W6 3.0 (4.0)
W10 4.5 (6.0)
20 Hilti, Inc. (US) 1-800-879-8000 | www.us.hilti.com I en español 1-800-879-5000 I Hilti (Canada) Corp. 1-800-363-4458 I www.hilti.ca I Product Technical Guide 2008
02_3.0_DX_Mod15.QXD:H440.04_03 DX.QXD
12/30/07
12:49 AM
Page 21
General Construction Fastening Systems
General Construction Fastener Design & Selection 3.2.1
3.2.1.1.6 Fastener Locations when Installing into Lightweight Concrete over Metal Deck Hilti Powder-Driven Fastener 3,000 psi Lightweight Concrete
12"
min. 3-1/4" 3" Form Deck Lower Flute Location Upper Flute Location
4-1/2" min.
Direction of shear load on fastener
4-1/2" min.
7-1/4" min.
1-1/8" Min. Edge Distance Direction of tension load on fastener
Figure 1 – Hilti Fastener Location in 3” Deep Composite Floor Deck Normal Deck Profile Orientation
Hilti Power-Driven Fastener 6"
3,000 psi Lightweight Concrete
Direction of shear load on fastener
Form Deck Upper Flute Location Lower Flute Location
Direction of tension load on fastener
7/8" Edge Distance
1-3/4"
min. 2-1/2"
1-1/2"
2-1/2" 3-1/2"
Figure 2 – Hilti Fastener Location in 1-1/2” Deep Composite Floor Deck Normal Deck Profile Orientation
Hilti Power-Driven Fastener 6"
3,000 psi Lightweight Concrete
Form Deck
min. 2-1/2"
Direction of shear load on fastener
Upper Flute Location Lower Flute Location
Direction of tension load on fastener
1-3/4" Edge Distance
1-3/4"
1-1/2" 3-1/2"
Figure 3 – Hilti Fastener Location in 1-1/2” Deep Composite Floor Deck Inverted Deck Profile Orientation
Hilti, Inc. (US) 1-800-879-8000 | www.us.hilti.com I en español 1-800-879-5000 I Hilti (Canada) Corp. 1-800-363-4458 I www.hilti.ca I Product Technical Guide 2008 21
02_3.0_DX_Mod15.QXD:H440.04_03 DX.QXD
12/30/07
12:49 AM
Page 22
General Construction Fastening Systems
3.2.1 General Construction Fastener Design & Selection 3.2.1.1.7 Bending Moments on Power-Actuated Fasteners in Concrete As with concrete anchors, bending moments on poweractuated fasteners installed in concrete and masonry base materials can be minimized through proper design detailing and installation practice. Proper design should include redundancy with multiple fastening points instead of singlepoint fastenings, in order to distribute bending moment effects amongst multiple fasteners. Installation of threaded rod coupler hangers on powder-actuated threaded studs should be done with the coupler run down over the stud shank and in contact with the concrete or masonry base material as depicted in the figure below. Care should be taken not to Arrangements to reduce or prevent moment on shank:
exceed the maximum torque discussed in Section 3.2.1.1.5. Although no design equations are provided for determining equivalent bending moment loads on power-actuated fasteners, recommended allowable bending moments are provided in the table below based on testing with a safety factor of 2:1 for static loading. Relatively small bending moments can contribute to a significant reduction in the overall fastening capacity and must be checked by the engineer.
Arrangement causing moment to act on shank:
Non-symmetric arrangement: • Moment on fastened part • Prying effect must be considered in determining loads acting on fastener
Coupler not tight against concrete Coupler tight against concrete
For information on concrete anchor bolt bending, reference Sections 4.1.8.4 and 4.1.9.8. Allowable Bending Moments For Threaded Stud Fasteners Installed in Minimum 2,000 psi Concrete1 Fastener Designation X-W6 X-CR W6 W10
Mrec ft-lb (Nm) 3.6 (4.9) 3.2 (4.3) 10.0 (13.6)
1 Based on a safety factor greater than or equal to 2.0.
3.2.1.1.8 Combined Loading of Power-Actuated Fasteners in Concrete Combined loading of power-actuated fasteners installed in concrete can be treated with exponent α = 1 unless otherwise provided for the specific application (e.g. ceiling clips with power-actuated fasteners with 45° loading).
(Ns / Nrec)α + (Vs / Vrec)α ≤ 1.0 where: Ns = Applied Tension Load Vs = Applied Shear Load
Nrec = Allowable Tension Load Vrec = Allowable Shear Load
3.2.1.1.9 Fastener Clamping & Nailhead Stand-Off Powder-actuated fastenings must be thought of in terms of a fastening system consisting of the powder-actuated tool, cartridges and the fastener itself. Not all powder-actuated fastening systems can achieve adequate embedment and proper clamping of the fastened part to the base material. The installer should start with the lowest power regulation and cartridge and work up until tight clamping is achieved. Installers should never “double-shoot” fastenings with
excessive nail head stand-off in order to drive them deeper. This can create a safety hazard and break the bond or sintering between the fastener shank and the base material.
22 Hilti, Inc. (US) 1-800-879-8000 | www.us.hilti.com I en español 1-800-879-5000 I Hilti (Canada) Corp. 1-800-363-4458 I www.hilti.ca I Product Technical Guide 2008
02_3.0_DX_Mod15.QXD:H440.04_03 DX.QXD
12/30/07
12:49 AM
Page 23
General Construction Fastening Systems
General Construction Fastener Design & Selection 3.2.1 3.2.1.1.10 DX Kwik System 3.2.1.1.10.1 Product Description DX-KWIK is a method of fastening into concrete that combines the speed and portability of powder-actuated fastenings with the performance and consistency of anchors. The DX-KWIK System requires a shallow, small diameter hole to be drilled into the concrete, then a powderactuated fastener is driven through the hole into the concrete. Product Features Two very important fastening principles are achieved by using the DX-KWIK System:
•
The fastener obtains its holding power in the concrete deeper than standard powder-actuated fastenings without pre-drilling
•
Concrete stresses are distributed deeper below the concrete surface
DX-KWIK Fasteners
DX-KWIK System Advantages •
Higher allowable loads
•
Ability to fasten into high-strength concrete
•
Virtually eliminates concrete surface spalls
•
More consistent fastening
TE 7 A Rotary Hammer Drill
DX 460 Powder-Actuated Fastening Tool
DX-Kwik
Anchor
Standard DX
3.2.1.1.10.2 Installation Instructions
23 mm
5 mm Ø
1. Drill a hole into the concrete using a TX-C 5/18 or TX-C 5/23 special DX-KWIK Bit.
2. Insert the special high strength fastener into the DX tool leaving the fastener point protruding out.
3. Using the required cartridge power drive the fastener into the concrete.
Note: • Typically, DX-KWIK Fasteners are 47 mm minimum in length. • As of publication date, only X-U and X-AL-H series fasteners have been tested. Reference Section 3.2.2.3 for allowable load capacity table.
Hilti, Inc. (US) 1-800-879-8000 | www.us.hilti.com I en español 1-800-879-5000 I Hilti (Canada) Corp. 1-800-363-4458 I www.hilti.ca I Product Technical Guide 2008 23
02_3.0_DX_Mod15.QXD:H440.04_03 DX.QXD
12/30/07
12:49 AM
Page 24
General Construction Fastening Systems
3.2.1 General Construction Fastener Design & Selection 3.2.1.2 Fastening to Steel 3.2.1.2.1 General Suitability A fastener driven into steel is influenced by the following factors:
When a powder or gas-actuated fastener is driven into steel, the steel around the fastener shank is displaced. This displaced steel flows back around the shank and into the knurling creating a keying hold or in the case of smooth shank fasteners a friction hold. In addition, the heat generated during the driving process, at temperatures of approximately 1650°F, causes partial fusion of the fastener to the steel.
•
Base steel thickness
•
Tensile strength of base steel
•
Fastener spacing and edge distance
•
Fastener shank diameter
3.2.1.2.2 Fastener Spacing, Edge Distance & Base Material Thickness Requirements for Steel Cmin = Min. Edge Distance = 1/2" (12 mm)1
Smin
Smin = Min. Fastener Spacing without reduction in performance = 1" (25 mm)1 t II = Min. Base Steel Thickness = 1/8" (3 mm)
Cmin
t II
1 Unless otherwise noted (e.g. X-BT fastener)
Base Steel Thickness
Holding Power
3.2.1.2.3 Base Steel Thickness and Fastener Driving Distance Requirements
Optimum Thickness 3/8" to 1/2" (10 to 12 mm)
Steel Thickness
Application Range for Standard Knurled Fasteners
Base Steel Tensile Strength (x1000) psi
Optimal holding power is obtained when fastener point is driven to distance h ET.
As the tensile strength of the base steel increases, the thickness of the base steel suitable for DX fastenings decreases.
Nail Type tI LS
hET
LS
hET
L S = hET + t I * The objective of this table is to ensure adequate through-penetration of the base steel. For load capacity of fasteners without through-penetration, refer to corresponding allowable load table and applicable footnotes for more details.
X-U X-EDNI X-EW6H-xx-9 EDS X-EGN X-EW10H-xx-14 X-DNI DS X-S13 P8THP X-S16 P8TH X-ZF X-CR X-AL-H
Recommended Driving Distance to Achieve Optimal Tension Capacity, h ET*
in. 0.394 - 0.551 0.394 - 0.551 0.315 - 0.433 0.472 - 0.669 0.315 - 0.433 0.512 - 0.630 0.591 - 1.063 0.669 - 1.063 0.394 - 0.472 > 0.433 0.591 - 1.063 > 0.394 0.591 - 1.063
mm 10 - 14 10 - 14 8 - 11 12 - 17 8-11 13 - 16 15 - 27 17 - 27 10-12 > 11 15 - 27 > 10 15 - 27
24 Hilti, Inc. (US) 1-800-879-8000 | www.us.hilti.com I en español 1-800-879-5000 I Hilti (Canada) Corp. 1-800-363-4458 I www.hilti.ca I Product Technical Guide 2008
02_3.0_DX_Mod15.QXD:H440.04_03 DX.QXD
12/30/07
12:49 AM
Page 25
General Construction Fastening Systems
General Construction Fastener Design & Selection 3.2.1
X-U
DNI
DS
X-AL-H
Wood Thickness (mm)
3.2.1.2.4 Recommended Fastener Lengths for Attaching Wood to Steel Base Material Application Limit X-U DNI Fasteners Application Limit Fasteners
Up to 1/4" (6 mm)
5/16" (8 mm) 3/8" (10 mm) 7/16" (11 mm) 1/2" (12 mm)
Base Material Thickness Notes: 1 X-U, DNI, DS or X-AL-H up to 62 mm long may be used in base steel up to 1/4" (6 mm) thick. 2 If the application limit is exceeded, shank buckling can occur. 3 Numbers in ● and ■ represent fastener length in mm.
3.2.1.2.5 Recommendations for Attaching Steel to Steel Base Material t I ≤ 1/8 in. (3 mm)
Note
1 Directly fastened material ≤ 1/8" thick usually deforms with the displaced base material. This allows a tight fit between the fastened steel and base material without the need for pre-drilling.
3.2.1.2.6 Maximum Tightening Torque Tightening-Torque
Tmax
Maximum Tightening Torque, Tmax, for Threaded Studs Driven into Steel, ft-lb (Nm) Stud Type Tmax
X-EW6H
X-EM8H
X-EW10H
X-CRM8
X-BT W10 & X-BT M8
3.0 (4.1)
8.0 (10.8)
11.0 (14.9)
6.0 (8.1)
6.0 (8.1)
Hilti, Inc. (US) 1-800-879-8000 | www.us.hilti.com I en español 1-800-879-5000 I Hilti (Canada) Corp. 1-800-363-4458 I www.hilti.ca I Product Technical Guide 2008 25
02_3.0_DX_Mod15.QXD:H440.04_03 DX.QXD
12/30/07
12:49 AM
Page 26
General Construction Fastening Systems
3.2.1 General Construction Fastener Design & Selection 3.2.1.2.7 Bending Moments on Power-Actuated Fasteners in Steel As with weld studs, bending moments on power-actuated fasteners installed in steel can be minimized through proper design detailing and installation practice. Proper design should include redundancy with multiple fastening points instead of single-point fastenings, in order to distribute bending moment effects amongst multiple fasteners. Installation of threaded rod coupler hangers on powder-actuated threaded studs should be done with the coupler run down over the stud shank and in contact with the steel base material as depicted in the figure below. Care should be taken not to exceed the maximum torque discussed in Section 3.2.1.2.6.
Arrangements to reduce or prevent moment on shank:
Although no design equations are provided for determining equivalent bending moment loads on power-actuated fasteners, recommended allowable bending moments are provided in the table below based on testing with a safety factor of 2:1 for static loading Relatively small bending moments can contribute to a significant reduction in the overall fastening capacity and must be checked by the engineer.
Arrangement causing moment to act on shank:
Non-symmetric arrangement: • Moment on fastened part • Prying effect must be considered in determining loads acting on fastener
Coupler not tight against steel
Coupler tight against steel
Allowable Bending Moments For Threaded Stud Fasteners Installed in Minimum ASTM A 36 Steel1 Fastener Nomenclature X-EW6H X-EM8H X-EW10H X-CRM8 X-BT M8/W10
Mrec ft-lb (Nm) 2.2 (3.0) 4.5 (6.2) 6.5 (8.8) 4.0 (5.5) 6.0 (8.2)
1 Based on a safety factor greater than or equal to 2.0.
3.2.1.2.8 Combined Loading of Power-Actuated Fasteners in Steel Combined loading of power-actuated fasteners installed in steel can be treated with exponent α = 1 unless otherwise provided for the specific application (e.g. powder-actuated fasteners for steel deck applications with diaphragm shear and tension uplift).
Hilti powder-actuated fasteners for attachment of steel decks (X-ENP-19 L15, X-EDN19 THQ12 and X-EDNK22 THQ12) have separate design equations for combined loading in the SDI Deck Diaphragm Design Manual, 3rd Edition (2006).
(Ns / Nrec)α + (Vs / Vrec)α ≤ 1.0 where: Ns = Applied Tension Load Vs = Applied Tension Load
Nrec = Allowable Tension Load Vrec = Allowable Tension Load
26 Hilti, Inc. (US) 1-800-879-8000 | www.us.hilti.com I en español 1-800-879-5000 I Hilti (Canada) Corp. 1-800-363-4458 I www.hilti.ca I Product Technical Guide 2008
02_3.0_DX_Mod15.QXD:H440.04_03 DX.QXD
12/30/07
12:49 AM
Page 27
General Construction Fastening Systems
General Construction Fastener Design & Selection 3.2.1 3.2.1.3 Power-Actuated Fastener Selection Guide
X-U Fastener
X-U MX Magazine
DS/EDS Fastener
X-ZF Fastener
X-ZF MX Fastener Collated
For universal, high quality fastenings to concrete and steel: perimeter wall applications, forming, underfloor, trunking, thin metal brackets, angles, etc. High-volume, repetitive fastenings to concrete and steel: perimeter wall applications, forming installation, etc.
A standard quality fastener for fastenings to concrete and CMU block
X-DNI/X-EDNI Fastener
For fastening to concrete (X-DNI) and steel (X-EDNI), forming, underfloor, trunking, installation straps, thin metal, brackets, angles, etc.
X-AL-H High-Strength Fastener
DX 600N
DX 76
DX 460
DX 36
Page Numbers
• • • • •
3.2.2 3.2.3 3.2.4
31-36 37-39 40-44
M
3.2.2 3.2.3 3.2.4
31-36 37-39 40-44
3.2.2 3.2.4
31-36 40-44
• • • • •
3.2.2
31-36
M
M
3.2.2
31-36
• • • • •
3.2.2
31-36
• • • • •
3.2.2
31-36
M
M
3.2.2
31-36
M
3.2.2
31-36
• • • • •
3.2.2
31-36
M
P10
• •
High volume repetitive fastenings to concrete and CMU block
Corrosion resistance equivalent to SAE 316 stainless steel for exterior or corrosive environments
X-EDNI MX Fastener Collated
2008 Product Technical Guide Section Numbers
For fastening to concrete (DS) and steel (EDS): perimeter wall applications, forming, underfloor, trunking, installation straps, thin metal, brackets, angles, etc.
X-CR Corrosion Resistant Fastener
X-DNI MX Fastener Collated
DX 351
•
DX 35
Fastener Notes: = Single M = Collated Fasteners (magazine required) P8 = 8 mm fastener guide required P10 = 10 mm fastener guide required Fastener Application
DX E72
Hilti Fastening Tool
High-volume, repetitive fastenings to concrete, forming installation, etc.
Fastenings to steel: angles, brackets, channels, tracks, etc.
For high performance fastening to high strength concrete and steel Note: Special drive piston is required
LiliNESA player NESA (NESAudio) is a logged audio format recorded by an emulator on Amiga called ANES. Made mostly obsolete by the NSF format. liliMacOS A demonstation of bitmapped graphics on NES.
liliMoby Shows the cover of Moby: Everything is Wrong in a neat (but buggy) pseudo-interlaced mode.
.What’s New in the Clean Slate 2.0.367 serial key or number?
Screen Shot
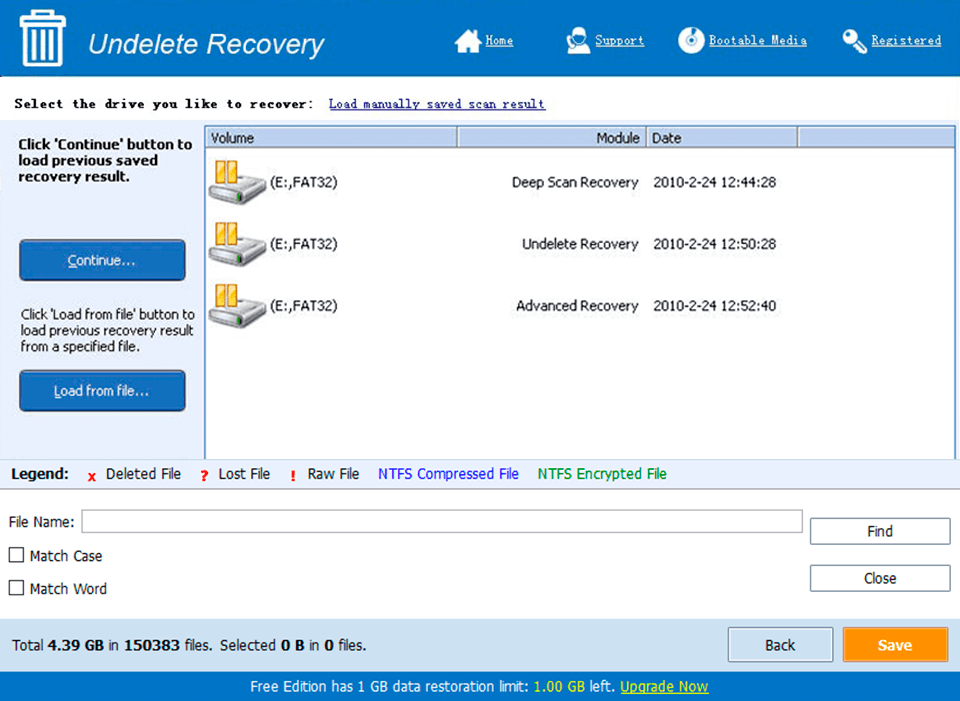
System Requirements for Clean Slate 2.0.367 serial key or number
- First, download the Clean Slate 2.0.367 serial key or number
-
You can download its setup from given links: